Factors Affecting the Performance and Lifetime of Activated Alumina
Table of Contents
Introduction
Activated alumina is a widely used adsorbent in various industries, but its performance and lifetime can be significantly influenced by several factors. This highly porous form of aluminum oxide has exceptional adsorption capabilities and is employed in applications such as water treatment, air drying, and catalyst support. To achieve optimal results and ensure cost-effectiveness, it’s crucial to understand the factors that can affect activated alumina’s performance and lifespan. In this article, we will discuss these factors, including operating conditions, impurities in the system, regeneration frequency, and proper handling and storage.
Operating Conditions
Temperature
The temperature of the operating environment directly impacts the adsorption capacity and efficiency of activated alumina. As temperature increases, the adsorption capacity of activated alumina generally decreases due to reduced adsorbate-adsorbent interactions. However, higher temperatures can improve desorption or regeneration efficiency, which is essential for maintaining the long-term performance of activated alumina. Consequently, it’s essential to monitor and control the temperature of the operating environment to ensure the most effective use of activated alumina in specific applications.
Humidity
Humidity levels in the environment play a crucial role in determining the moisture adsorption capacity of activated alumina. In applications such as air drying or water treatment, higher humidity levels result in increased moisture adsorption. However, excessively high humidity can lead to reduced performance, as the alumina becomes saturated with moisture and loses its ability to adsorb other contaminants. On the other hand, low humidity environments can result in underutilization of activated alumina’s adsorption capacity. Balancing humidity levels is critical for optimizing the performance and longevity of activated alumina.
Flow Rate
The flow rate of the fluid or gas passing through the activated alumina bed affects its adsorption performance and lifetime. High flow rates can reduce the contact time between the alumina and the contaminants, leading to decreased adsorption efficiency. Conversely, low flow rates can result in increased pressure drop across the bed and may cause channeling, a phenomenon where fluid or gas flows through preferential pathways, bypassing the majority of the alumina. To optimize the performance and longevity of activated alumina, it’s essential to maintain the appropriate flow rate for specific applications.
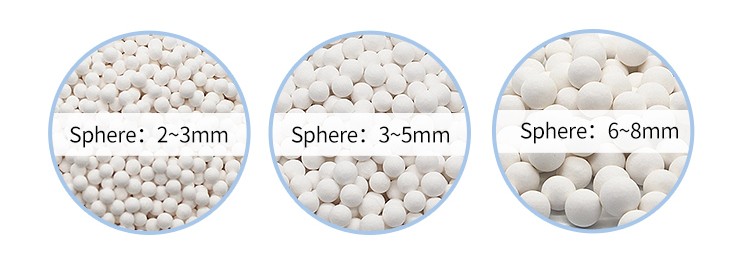
Impurities in the System
Particulate Matter
The presence of particulate matter in the fluid or gas being treated can lead to fouling and reduced performance of activated alumina. Particulates can clog the pores of the alumina, limiting its adsorption capabilities and decreasing its overall effectiveness. To address this issue, pre-filtration methods can be employed to remove particulate matter before the fluid or gas reaches the activated alumina bed. This will help maintain the adsorption capacity of the alumina and prolong its useful life.
Chemical Contaminants
Certain chemical contaminants can negatively impact the adsorption properties of activated alumina, reducing its efficiency and lifetime. For instance, the presence of strong acids or alkalis can react with the alumina, altering its surface properties and diminishing its adsorption capacity. In some cases, these contaminants may also lead to the dissolution or degradation of the alumina. To minimize the effects of chemical contaminants on activated alumina performance, it’s crucial to monitor and control their concentration in the system.
Regeneration Frequency and Process
Regeneration Frequency
The frequency of regeneration, or the process of removing adsorbed contaminants, is a key factor in maintaining the performance and extending the lifetime of activated alumina. Over time, activated alumina becomes saturated with adsorbed contaminants, reducing its effectiveness. Regular regeneration helps restore the adsorption capacity of the alumina, ensuring its continued performance. However, excessive regeneration can cause structural damage to the alumina, shortening its useful life. Therefore, it’s essential to establish an appropriate regeneration schedule based on the specific application and operating conditions.
Regeneration Process
The regeneration process for activated alumina typically involves heating the material to a high temperature, which drives off the adsorbed contaminants, restoring its adsorption capacity. However, improper regeneration methods or temperatures can damage the alumina, decreasing its performance and reducing its lifespan. It’s crucial to follow the manufacturer’s guidelines and best practices for regeneration to ensure the continued effectiveness and longevity of activated alumina.
Proper Handling and Storage
Handling
Activated alumina is a robust and durable material, but improper handling can result in damage that compromises its performance and lifetime. To prevent breakage, chipping, or crushing of the alumina, it’s essential to handle it with care during transportation, installation, and maintenance. Avoid dropping or applying excessive force to the alumina to preserve its structural integrity and adsorption capabilities.
Storage
Proper storage is vital for maintaining the performance and lifetime of activated alumina. When not in use, activated alumina should be stored in a cool, dry, and well-ventilated area, away from direct sunlight and extreme temperature fluctuations. Exposure to moisture or contaminants during storage can reduce the alumina’s adsorption capacity and effectiveness, leading to suboptimal performance and decreased lifespan. By following proper storage guidelines, you can help ensure the long-term success of your activated alumina.
Maximizing Activated Alumina Performance: Key Takeaways
Activated alumina is an invaluable adsorbent material in various industries due to its exceptional adsorption properties. However, to ensure optimal performance and prolong its useful life, it’s essential to understand and manage the factors that can influence its effectiveness. By carefully controlling the operating conditions, monitoring impurities in the system, implementing proper regeneration practices, and adhering to appropriate handling and storage guidelines, you can maximize the performance and lifetime of activated alumina in your specific application.
FAQs
How does temperature affect the performance of activated alumina?
As temperature increases, the adsorption capacity of activated alumina generally decreases due to reduced adsorbate-adsorbent interactions. However, higher temperatures can improve desorption or regeneration efficiency.
How does humidity impact activated alumina performance?
Humidity levels directly influence the moisture adsorption capacity of activated alumina. Higher humidity levels result in increased moisture adsorption, while excessively high humidity can lead to reduced performance due to saturation.
How can I improve the performance and lifespan of activated alumina in my system?
By carefully controlling the operating conditions, monitoring impurities in the system, implementing proper regeneration practices, and adhering to appropriate handling and storage guidelines, you can maximize the performance and lifetime of activated alumina in your specific application.
Does activated alumina have a shelf life?
Activated alumina does not have a specific shelf life. However, proper storage conditions, such as a cool, dry, and well-ventilated area away from direct sunlight and extreme temperature fluctuations, are essential to maintain its adsorption capacity and effectiveness.
Can you reuse activated alumina?
Yes, activated alumina can be regenerated and reused multiple times. The regeneration process typically involves heating the material to a high temperature, which drives off the adsorbed contaminants and restores its adsorption capacity.
How do you recharge activated alumina?
To recharge activated alumina, the regeneration process involves heating the material to a high temperature (usually between 250°F to 350°F or 121°C to 177°C) for several hours. This process drives off the adsorbed contaminants, effectively restoring the adsorption capacity of the activated alumina.
How often should desiccant be replaced?
The replacement frequency of a desiccant, such as activated alumina, depends on various factors like operating conditions, humidity levels, and the specific application. Generally, desiccant replacement is necessary when its adsorption capacity is significantly reduced or when the material shows signs of degradation.
What is the shelf life of alumina powder?
Alumina powder does not have a specific shelf life. However, proper storage conditions, such as a cool, dry, and well-ventilated area away from direct sunlight and extreme temperature fluctuations, are necessary to maintain its quality and effectiveness.
At what temperature does alumina degrade?
Alumina, or aluminum oxide (Al2O3), has a high melting point of approximately 3,762°F (2,072°C) and is stable at high temperatures. However, the specific temperature at which alumina degrades depends on the type of alumina and its purity. It’s important to consult the manufacturer’s guidelines for the specific alumina product to determine its temperature stability and degradation point.
The Potential of Activated Alumina Powder: Applications and Advantages
The Regeneration Process of Activated Alumina: Techniques and Best Practices