Choosing the Right Desiccant for Compressed Air Systems: A Comparison of Activated Alumina, Silica Gel, and Molecular Sieves
Desiccant | Pros | Cons |
---|---|---|
Activated Alumina | High reusability, chemical stability, cost-effective | May not achieve extremely low dew points |
Silica Gel | High moisture adsorption capacity | Limited reusability compared to others |
Molecular Sieves | Ideal for very low dew points | Higher cost, specific regeneration needs |
Table Of Contents
“Moisture in compressed air can be more damaging than you think; it’s the silent destroyer of efficiency and equipment reliability.”
Introduction
Selecting the right desiccant for compressed air systems is crucial for maintaining efficiency and air quality. Moisture control in compressed air systems is often overlooked, but the consequences of excessive moisture can be costly and damaging. Whether you’re dealing with rusted pipelines, unreliable machinery, or contaminated end products, the impact of poor moisture management can be devastating.
To tackle this issue, the choice of desiccant becomes essential. Activated alumina, silica gel, and molecular sieves are the three most commonly used desiccants for moisture removal in compressed air systems. Each of these materials has unique properties that make them suitable for different environments and requirements. In this post, we will explore their features, advantages, and drawbacks to help you make an informed decision.
Moisture control is not just about protecting equipment—it’s about optimizing performance, reducing downtime, and cutting costs. Let’s dive into the world of desiccants for compressed air systems and find out which one might be right for your needs.
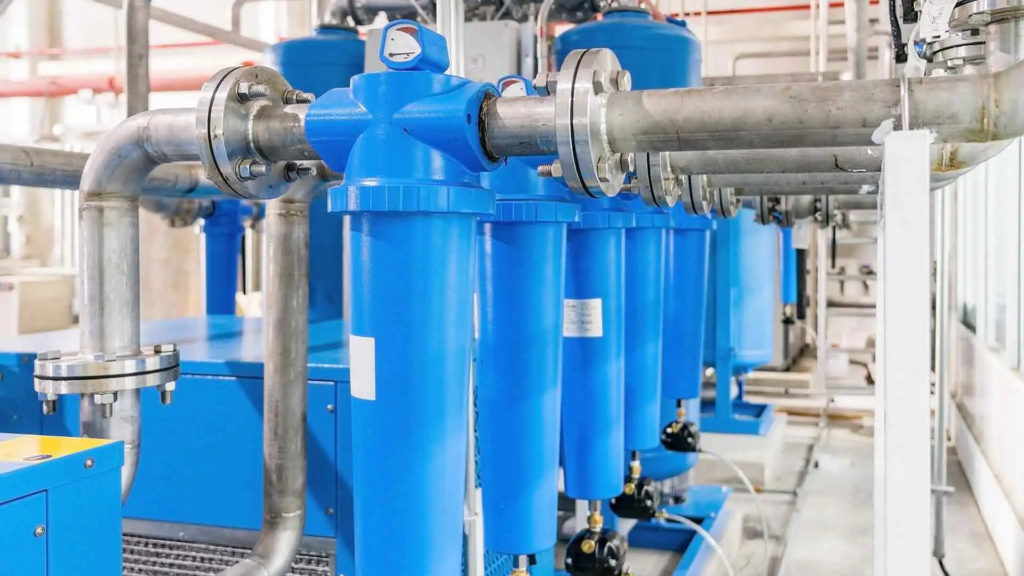
Why Moisture Control Matters in Compressed Air Systems
Moisture in compressed air is more than just an inconvenience—it’s a potential disaster waiting to happen. When moisture gets into a compressed air system, it can lead to rust in the piping, causing leaks and weakening the overall structure. This can result in costly repairs or even the need to replace significant parts of the system. Furthermore, moisture can cause blockages, compromising the performance of pneumatic tools and machinery that rely on clean, dry air.
Problem Caused by Moisture | Impact |
Corrosion | Moisture leads to rust, weakening infrastructure and causing leaks. |
Contamination | Moisture can introduce contaminants, affecting product quality in industries like food. |
Reduced Efficiency | Moisture affects tool performance, increasing energy consumption and operational costs. |
Moisture can also lead to contamination in sensitive environments. For industries like food processing, pharmaceuticals, or electronics, even trace amounts of moisture can degrade product quality or cause complete product failure. Moisture in compressed air can introduce unwanted contaminants that affect the consistency and safety of products, leading to customer dissatisfaction and regulatory issues.
Effective moisture control ensures not only the longevity of your compressed air systems but also maintains the quality of the end products. By using a proper desiccant, you can keep the air dry, minimize downtime, and maximize the efficiency of your operations. Moisture control directly contributes to energy efficiency, as dry air reduces resistance within the system, leading to lower energy consumption.
Types of Desiccants for Compressed Air Systems
Let’s explore the key players when it comes to moisture control in compressed air systems. There are several types of desiccants commonly used to keep compressed air systems dry, but the most popular ones are activated alumina, silica gel, and molecular sieves. Each of these desiccants has specific properties that make them suitable for different applications, and understanding their differences is key to choosing the right one.
Desiccant Type | Primary Function |
Activated Alumina | High surface area for moisture adsorption; ideal for general industrial use. |
Silica Gel | Rapid moisture adsorption; useful in moderate dew point environments. |
Molecular Sieves | Selective adsorption for extremely low dew points; suitable for precision applications. |
Activated alumina is a highly porous form of aluminum oxide with excellent moisture adsorption capabilities. It works by capturing water molecules on its surface, making it an ideal choice for many standard industrial applications. Silica gel, on the other hand, is perhaps the most well-known desiccant and is widely used for its high moisture adsorption capacity. It’s especially useful for applications that do not require extremely low dew points.
Molecular sieves are the precision tools of the desiccant world. They have extremely small and uniform pore sizes, allowing them to selectively adsorb water molecules even when the air needs to reach very low dew points. While molecular sieves are highly effective, they are also more costly, making them a specialized choice for applications where precise moisture control is critical.
Activated Alumina Desiccant: Pros and Cons
Activated alumina is a tried-and-true desiccant for compressed air systems, and for good reasons. Activated alumina works through an adsorption process, where moisture is captured and held on the large surface area of its porous granules. This makes it highly effective for drying air in industrial systems where moderate dew points are acceptable. One of the main benefits of activated alumina is its reusability—after it becomes saturated with moisture, it can be regenerated by heating, allowing it to be reused multiple times.
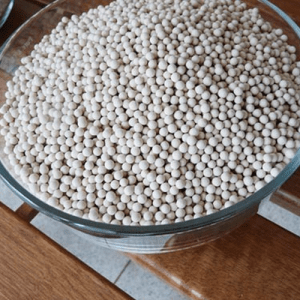
Advantage | Explanation |
Reusable | Activated alumina can be regenerated, reducing replacement costs. |
High Efficiency | Its large surface area allows for significant moisture adsorption capacity. |
Versatility | Can be used in various applications, including gas dehydration, air drying, and purification. |
The chemical stability of activated alumina also makes it a favorable choice for many industrial settings. It does not react with most chemicals, meaning it remains effective even in environments where other substances are present. This makes it an excellent choice for air quality management, as it ensures that the air remains uncontaminated while moisture is effectively removed.
However, activated alumina may not always be the best choice if extremely low dew points are required. Its adsorption capacity, while high, does not match that of molecular sieves for precision drying. For applications where achieving very low moisture levels is critical—such as in electronics or pharmaceutical manufacturing—other options may be more suitable.
Silica Gel for Compressed Air: Pros and Cons
Silica gel may be more commonly associated with those little packets in product boxes, but it’s also a powerful desiccant for compressed air. Silica gel is a granular, vitreous, and porous form of silicon dioxide that works by adsorbing water molecules onto its surface. It has a high moisture adsorption capacity, which makes it effective for drying compressed air in a wide range of industrial applications.
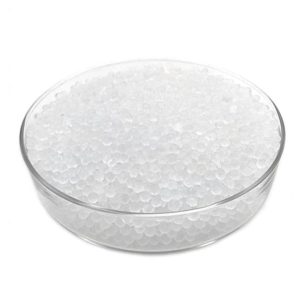
Advantage | Explanation |
High Moisture Adsorption | Silica gel can quickly adsorb large quantities of moisture, making it highly effective for drying. |
Simple Use | Easy to use and available in various forms, suitable for a wide range of environments. |
Limited Reusability | It can be regenerated, but its performance degrades over time compared to activated alumina. |
One of the main advantages of silica gel is its ability to rapidly adsorb large quantities of moisture. This makes it particularly suitable for situations where quick and effective drying is needed. Silica gel also works well in environments where dew points are moderate, and it’s a great option for general-purpose air drying in applications like packaging or food storage.
However, silica gel does have its drawbacks. Unlike activated alumina, silica gel has limited reusability. It can be regenerated, but its effectiveness decreases with each regeneration cycle, making it a less cost-effective solution for applications that require continuous moisture control. Additionally, silica gel may not achieve the ultra-low dew points that molecular sieves are capable of reaching, which limits its use in some specialized environments.
“Selecting the right desiccant is not just about moisture removal; it’s about striking the perfect balance between cost, efficiency, and operational needs.”
Molecular Sieves: Pros and Cons
Molecular sieves are like the precision tools of the desiccant world. They are synthetic crystalline materials with extremely small and uniform pore sizes, which allow them to adsorb water molecules even when precise control is required. Molecular sieves are particularly effective at achieving very low dew points, making them a preferred choice in applications where dry air is critical to prevent any moisture-related issues.
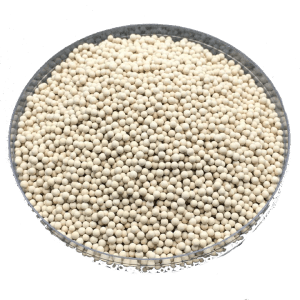
Advantage | Explanation |
Precise Moisture Control | Capable of achieving very low dew points, ideal for critical applications. |
Selective Adsorption | Molecular sieves only adsorb molecules of specific sizes, ensuring effective moisture removal. |
High Cost | More expensive compared to other desiccants, suitable for highly specialized environments. |
The main advantage of molecular sieves is their specificity. Their small pores selectively trap only molecules of certain sizes, which allows them to adsorb moisture while ignoring other gases. This makes molecular sieves particularly effective for industrial drying solutions that require exact control over moisture levels, such as chemical processing or gas dehydration. They are also capable of working at both high and low temperatures, which adds to their versatility.
However, molecular sieves are generally more expensive than other desiccants, both in terms of initial cost and ongoing maintenance. They also require more specific regeneration conditions, which can add complexity to the operation. Due to these factors, molecular sieves are often reserved for highly specialized applications where their unique properties outweigh their higher costs.
Comparing Desiccant Efficiency and Cost
Choosing a desiccant comes down to balancing efficiency with cost. Each of the desiccants—activated alumina, silica gel, and molecular sieves—has different levels of efficiency when it comes to moisture adsorption. Activated alumina offers high adsorption efficiency for general industrial applications and has the advantage of being reusable, which makes it cost-effective over the long term. Its combination of moderate cost and good performance makes it a popular choice for many standard compressed air drying solutions.
Desiccant | Efficiency | Cost | Ideal Application |
Activated Alumina | Moderate efficiency, reusable | Moderate cost, cost-effective | General industrial air drying solutions. |
Silica Gel | High efficiency, rapid adsorption | Low to moderate cost | Packaging, short-term air drying needs. |
Molecular Sieves | Very high efficiency, precise control | High cost | Specialized applications requiring low dew points. |
Silica gel also has a high moisture adsorption capacity, which makes it efficient in the short term. However, due to its limited reusability, the overall cost can be higher in applications requiring continuous drying. It’s a good option for smaller-scale or less frequent use, where regeneration is not a significant factor. On the other hand, molecular sieves have the highest adsorption efficiency, particularly for applications that require extremely low dew points. Their precision makes them effective, but their higher cost often restricts their use to specialized environments.
When evaluating which desiccant is the most cost-effective, it’s essential to consider not just the initial cost but also the ongoing maintenance, reusability, and specific needs of your compressed air system. If you require very low dew points, molecular sieves may justify their higher cost. However, for general-purpose moisture removal where cost and efficiency are both considerations, activated alumina often emerges as the best choice.
Selecting the Best Desiccant for Your Needs
The right desiccant depends on your specific system needs and operational requirements. When selecting a desiccant for compressed air systems, you need to consider factors like the required dew point, the operating environment, and your budget. Activated alumina is often the best desiccant for air systems that require moderate dew points and long-term cost efficiency. Its reusability makes it an attractive choice for operations looking to minimize ongoing costs.
Silica gel may be more suitable if you need a quick and effective moisture adsorption solution but do not require very low dew points. It works well for applications like packaging, where rapid drying is needed but reusability is less of a concern. For specialized applications that require extremely precise control over moisture levels, molecular sieves are the best choice. Although they are more expensive, their ability to achieve ultra-low dew points makes them indispensable in certain environments.
In the end, choosing the right desiccant means matching the properties of the desiccant with the needs of your specific application. Evaluate your system’s requirements, consider the pros and cons of each desiccant, and make a decision that balances both performance and cost. Whether it’s activated alumina, silica gel, or molecular sieves, selecting the right desiccant will ensure your compressed air system remains efficient and effective.
One of the key challenges I often see is industries struggling with balancing cost-effectiveness with performance when selecting a desiccant for compressed air systems. Activated alumina, silica gel, and molecular sieves each have distinct advantages, but knowing which desiccant aligns best with specific operational needs can be daunting. Addressing this challenge requires understanding not just the moisture control needs but also evaluating long-term costs, maintenance requirements, and the desired dew point. Providing practical guidance and tailoring solutions to individual system needs has proven crucial in making the right choice.
Real-World Examples: How Industries Use Different Desiccants
Different industries have different needs, and that means choosing the right desiccant isn’t a one-size-fits-all decision. In the food and beverage industry, for example, silica gel is often used to maintain product quality by keeping packaging environments dry. Its ability to quickly adsorb moisture makes it ideal for situations where packaging needs to stay moisture-free to preserve the quality of food items.
In the chemical processing industry, molecular sieves are frequently used to achieve the very low dew points required for specific chemical reactions. Their precision in moisture adsorption ensures that no residual moisture affects the chemical properties of the end product, which is crucial for quality control. In contrast, activated alumina is widely used in industrial air treatment applications, where maintaining moderate dew points is sufficient for protecting equipment and ensuring system reliability.
These examples highlight how different desiccants fit different scenarios based on the unique demands of each industry. While silica gel is excellent for quick, one-time moisture adsorption, molecular sieves provide unmatched precision, and activated alumina offers a balance of cost-efficiency and performance for ongoing operations. Each desiccant plays a vital role in maintaining compressed air quality in different industrial settings.
I remember working with a manufacturing facility that struggled with maintaining product quality due to moisture contamination. Initially, they were using silica gel, but it couldn’t achieve the required low dew points. After assessing their needs, we switched to molecular sieves, and the difference was immediate—production downtime was minimized, and the quality of their output improved significantly. The precision of molecular sieves allowed them to reach the extremely low moisture levels needed, ultimately saving significant costs related to waste and product recalls. See also: The Science Behind PSA: How Pressure Swing Adsorption Powers Our Industries
Frequently Asked Questions
What is the best desiccant for compressed air systems?
The best desiccant for compressed air systems depends on your needs. Activated alumina is cost-effective for moderate dew points, silica gel is great for quick moisture adsorption, and molecular sieves are ideal for extremely low dew points.
How does activated alumina desiccant work?
Activated alumina works by adsorbing moisture through its porous surface, which traps water molecules and effectively dries compressed air. It can be regenerated, making it reusable and cost-effective.
What are the advantages of using silica gel for compressed air drying?
Silica gel has a high moisture adsorption capacity and works quickly to absorb moisture, making it effective for drying compressed air where rapid results are needed. However, it has limited reusability compared to other desiccants.
When should I choose molecular sieves over other desiccants?
Molecular sieves are ideal for applications that require extremely low dew points and precise moisture control. Their uniform pore size allows them to selectively adsorb moisture, making them perfect for specialized environments.
How do I decide which desiccant is best for my industrial application?
Consider factors such as desired dew point, operating environment, and budget. Activated alumina is versatile, silica gel is best for rapid drying, and molecular sieves provide precision for low dew points.
What are the limitations of silica gel vs. activated alumina?
Silica gel is effective for quick moisture adsorption but has limited reusability compared to activated alumina. Activated alumina can be regenerated multiple times, making it more cost-effective for continuous use.
How do molecular sieves differ from other desiccants?
Molecular sieves have precise pore sizes that allow them to selectively adsorb water molecules. This makes them ideal for applications requiring extremely low moisture levels, whereas other desiccants may not achieve the same precision.
What are the cost considerations for choosing a desiccant?
Activated alumina is typically cost-effective due to its reusability. Silica gel has a lower initial cost but higher maintenance in long-term use. Molecular sieves are the most expensive, but they provide precise moisture control.
Can I regenerate silica gel desiccant?
Yes, silica gel can be regenerated by heating. However, its adsorption efficiency decreases after each regeneration cycle, making it less effective over time compared to activated alumina.
How does moisture affect compressed air systems?
Moisture in compressed air can lead to corrosion, contamination, and reduced efficiency, which can damage equipment, increase energy costs, and degrade product quality.
Why is activated alumina a popular choice for industrial air treatment?
Activated alumina’s chemical stability, high adsorption capacity, and reusability make it an ideal choice for industrial air treatment. It maintains air quality and provides effective moisture control for various industrial applications.
What role do molecular sieves play in compressed air treatment?
Molecular sieves remove moisture with precision, achieving extremely low dew points. They are ideal for compressed air systems where maintaining very low moisture content is crucial, such as in electronics manufacturing.
How efficient is activated alumina compared to molecular sieves?
Activated alumina is efficient for moderate moisture removal and is cost-effective due to its reusability. Molecular sieves, however, are more efficient for extremely low moisture levels, providing precise control where needed.
What are the common types of desiccants used for compressed air systems?
The most common types of desiccants are activated alumina, silica gel, and molecular sieves. Each has distinct properties suitable for different moisture control requirements.
How do I know when to regenerate the desiccant in my system?
You should regenerate your desiccant when its adsorption capacity decreases, typically indicated by increased moisture levels in the compressed air. Monitoring dew points can help determine when regeneration is needed.
Which desiccant is best for achieving the lowest possible dew point?
Molecular sieves are best for achieving the lowest possible dew points. Their precise adsorption capability allows them to achieve extremely low moisture levels, making them ideal for critical applications.
Can I use silica gel for moisture control in food packaging?
Yes, silica gel is often used for moisture control in food packaging because of its ability to quickly adsorb moisture and prevent spoilage. It helps maintain product quality by keeping the packaging environment dry.
How does moisture adsorption efficiency vary among different desiccants?
Moisture adsorption efficiency depends on the desiccant type. Molecular sieves have the highest efficiency for low dew points, while silica gel works quickly but is less reusable. Activated alumina strikes a balance between efficiency and reusability.
What is the main difference between adsorption and absorption in desiccants?
Adsorption involves moisture being captured on the surface of the desiccant, whereas absorption involves moisture being soaked into the material. Desiccants like activated alumina and silica gel work through adsorption.
What are the maintenance requirements for desiccant-based compressed air drying solutions?
Maintenance includes monitoring moisture levels, regenerating the desiccant as needed, and ensuring optimal operating conditions, such as maintaining the correct air flow rate and temperature for effective adsorption.
Conclusion
Choosing the right desiccant for compressed air systems can be the difference between smooth operations and unexpected breakdowns. Activated alumina, silica gel, and molecular sieves each have unique properties that make them suitable for different environments and requirements. Understanding their strengths and limitations is key to making the right choice.
With the rise of more energy-efficient and sustainable technologies, I see desiccants like activated alumina, silica gel, and molecular sieves becoming increasingly specialized to meet advanced industrial needs. As industries push for greater efficiency, I believe we’ll see enhanced versions of these desiccants designed to optimize adsorption capacity while minimizing regeneration energy requirements. This evolution will also involve smart sensors integrated into systems to better monitor and manage the moisture levels, ensuring that the most effective desiccant is always being used under the right conditions.
Evaluate your system’s specific needs—whether it’s moderate dew points, very low moisture levels, or cost-effective long-term use—and select the desiccant that aligns best with your operational goals. Activated alumina often offers the best balance of performance and cost, but silica gel and molecular sieves have their own specialized roles that can’t be overlooked. For more information, explore our offerings in Activated Alumina and Molecular Sieves.
To learn more about optimizing compressed air systems, check out our previous post: Optimizing Compressed Air Systems with Activated Alumina: Moisture Control for Better Efficiency and Activated Alumina for Sulfur Removal in Refining Processes.
For a deeper dive into desiccant technologies, refer to A Complete Guide to Activated Alumina and A Complete Guide to Molecular Sieves. If you’re ready to choose a product, explore our Activated Alumina for reliable moisture control.
Review of Desiccant in the Drying and Air-Conditioning Application