Gas Separation with Molecular Sieves
Feature | Description |
---|---|
Gas Separation | Molecular sieves are crucial for efficient gas separation, particularly in applications like PSA oxygen production. |
Types Used | Common molecular sieves for gas separation include 3A, 4A, 5A, 13X, and MSOX-500/MSOX-501. |
High Efficiency | Offers high selectivity and efficiency in separating gases, which is essential for industrial applications. |
Product Options | Explore different molecular sieve products for your specific gas separation needs here. |
Table of Contents
Introduction
Molecular sieves are incredibly versatile materials that have a wide range of applications in various industries. They excel in removing moisture and other contaminants from liquid and gas streams, making them ideal for gas separation processes.
In this article, we will discuss the properties of molecular sieves, their types, and their applications in different industries. We will also compare the performance of different types of molecular sieves and provide real-world examples of their use.
Properties of Molecular Sieves
Molecular sieves are crystalline aluminosilicates with unique properties that make them perfect for gas separation and purification processes. They have a well-defined pore structure, allowing them to selectively adsorb molecules based on their size, shape, and affinity for the sieve surface.
The crystalline composition of molecular sieves enables them to create virtually moisture-free products, making them particularly useful in gas dehydration and desulfurization operations. They can also be regenerated by heating them to optimal temperatures ranging from 130°C to 350°C, depending on the sieve type.
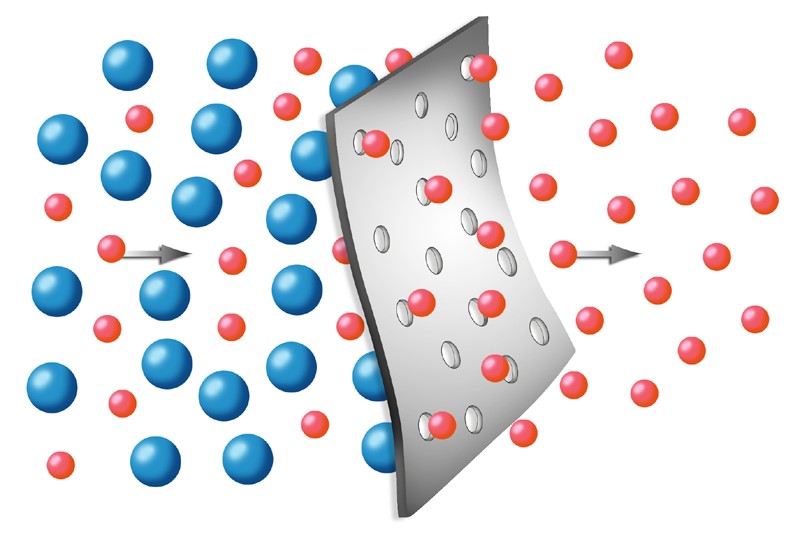
Types of Molecular Sieves
There are several types of molecular sieves, with the most common being Molecular Sieves 3A, Molecular Sieves 4A, Molecular Sieves 5A, and Molecular Sieves 13X (also known as Molecular Sieves 10A). Each type has a unique pore diameter, allowing for selective adsorption of specific molecules.
Molecular Sieve | Pore Diameter | Applications |
---|---|---|
3A | 3 Å | Drying polar liquids like ethanol and methanol; drying propylene, butadiene, and acetylene |
4A | 4 Å | Static drying in gas and liquid streams, electronics and electric systems, medicine and diagnostic kit packaging, perishable food items, and chemical packaging |
5A | 5 Å | Removal of mercaptans, CO2, and H2S from natural gas; separation of normal paraffins from cyclic and branched chain hydrocarbons |
13X (10A) | 10 Å | Separation of oxygen and nitrogen from air streams, oxygen generation, mercaptan removal from natural gas, insulating glass units |
Applications of Molecular Sieve in Gas Separation
Drying Ethanol with Molecular Sieves
One of the most common applications of molecular sieves is in the drying of ethanol. Ethanol is a versatile solvent used in various industries, but it must be free of moisture to be effective. Molecular sieves can efficiently remove water molecules from ethanol, ensuring its purity and effectiveness.
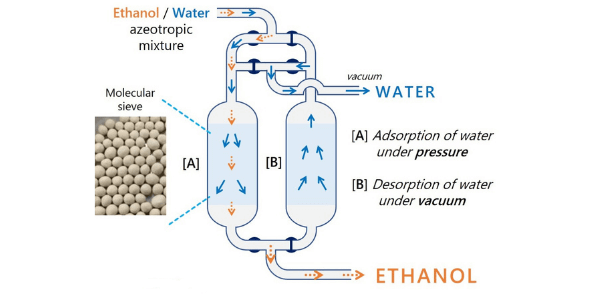
Methanol Purification with Molecular Sieves
Methanol is another essential compound in numerous industries, and its purity is crucial for its various applications. Molecular sieves can effectively remove impurities, such as water and other contaminants, from methanol, ensuring a high-quality product.
Molecular Sieve Column Design
A critical aspect of using molecular sieves in gas separation processes is the design of the molecular sieve column. Proper column design ensures optimal adsorption and desorption, which ultimately leads to efficient gas separation. Factors to consider when designing a molecular sieve column include the type of sieve, its size, and the specific process conditions.
Molecular Sieve Dehydration Unit
Molecular sieve dehydration units are commonly used in industries like oil and gas, where removing water from streams is essential. These units use molecular sieves to selectively adsorb water molecules, leaving behind a dry gas or liquid product.
Molecular Sieve Design Considerations
When designing a molecular sieve system, several factors must be considered, including the choice of sieve material, pore size, and operating conditions. The right combination of these factors will lead to an efficient and cost-effective gas separation process.
Gas Separation and Other Key Molecular Sieve Processes
Gas separation is just one of several essential molecular sieve processes that enhance purity and efficiency in various industries. Alongside gas separation, molecular sieves are vital in processes such as adsorption, gas drying, and catalytic support, each designed to tackle specific industrial challenges.
To explore the full range of processes enabled by molecular sieves and understand how they contribute across different industries, visit our comprehensive guide on Key Molecular Sieve Processes.
Molecular Sieve Regeneration
One of the key advantages of using molecular sieves is their ability to be regenerated and reused multiple times. Regeneration involves removing the adsorbed molecules from the molecular sieve, typically through a combination of heat and pressure. This process restores the adsorption capacity of the molecular sieve, allowing it to be used for additional cycles.
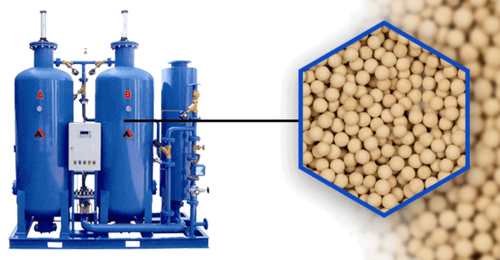
Comparison of 3A, 4A, and 5A Molecular Sieves
Property | 3A | 4A | 5A |
---|---|---|---|
Pore Diameter (Å) | 3 | 4 | 5 |
Molecular Formula | K12[(AlO2)12(SiO2)12] · nH2O | Na12[(AlO2)12(SiO2)12] · nH2O | Ca4.5[(AlO2)12(SiO2)12] · nH2O |
Main Application | Drying polar liquids and gases | Static drying in various industries | Removal of contaminants from natural gas |
Real-World Examples and Case Studies
Industry | Application | Molecular Sieve Type |
---|---|---|
Natural Gas | Dehydration | 3A, 4A, 5A, 13X |
Petrochemical | Ethylene production | 3A |
Air Separation | Oxygen and nitrogen separation | 13X |
Refrigeration | Drying refrigerant gases | 3A |
Pharmaceutical | Solvent drying and purification | 3A, 4A, 5A |
Insulating Glass | Moisture control in sealed units | 3A |
Automotive | Drying air in compressed air brake systems | 4A |
Comparison with Other Adsorbents
Molecular sieves offer several advantages over other types of adsorbents, such as activated carbon, silica gel, and alumina. The table below compares the main features of these adsorbents.
Adsorbent | Adsorption Capacity | Selectivity | Regeneration | Mechanical Strength |
---|---|---|---|---|
Molecular Sieve | High | High | Easy | High |
Activated Carbon | Moderate | Low | Moderate | Moderate |
Silica Gel | Low | Low | Moderate | Moderate |
Alumina | Low | Low | Moderate | Moderate |
As shown in the table, molecular sieves have a higher adsorption capacity, selectivity, and mechanical strength compared to other adsorbents. They are also easier to regenerate, making them a more efficient and cost-effective choice for many applications.
Advancements in Molecular Sieve Technology
As industries continue to evolve and demand for more efficient and sustainable processes increases, molecular sieve technology has seen significant advancements. These innovations have led to the development of more effective molecular sieves with enhanced performance, longer lifespans, and reduced energy consumption.
High-performance Molecular Sieves
Recent advancements in molecular sieve technology have resulted in the creation of high-performance molecular sieves. These advanced sieves offer superior adsorption capacities and selectivities, allowing for more efficient gas separation processes. High-performance molecular sieves can be tailored to specific applications, ensuring the best possible results for each unique process.
Hybrid Molecular Sieves
Another emerging trend in molecular sieve technology is the development of hybrid molecular sieves. These materials combine the properties of different types of molecular sieves or other adsorbents to achieve enhanced performance. Hybrid molecular sieves can offer improved selectivity, adsorption capacity, and resistance to contaminants, making them a valuable option for various gas separation applications.
Energy-efficient Molecular Sieve Processes
Energy efficiency has become a priority in many industries, and molecular sieve technology is no exception. Innovations in molecular sieve processes have focused on reducing energy consumption, both during the adsorption and regeneration stages. These energy-efficient processes can lead to significant cost savings and reduced environmental impact, making them an attractive option for industries looking to minimize their energy footprint.
Future Prospects of Molecular Sieve Technology
The future of molecular sieve technology is expected to see continued advancements and growth, driven by increasing demand for efficient gas separation solutions in various industries. Some potential areas of development include:
Nanoscale Molecular Sieves
The development of nanoscale molecular sieves could revolutionize gas separation processes by offering unprecedented selectivity and adsorption capacities. These materials would be capable of separating gas mixtures at the molecular level, leading to ultra-efficient gas separation processes.
Smart Molecular Sieves
Smart molecular sieves are another area of potential development. These materials could be engineered to respond to specific environmental conditions or stimuli, adjusting their adsorption properties accordingly. This adaptability could lead to more efficient and versatile gas separation processes.
Biodegradable Molecular Sieves
With increasing concerns about the environmental impact of industrial processes, the development of biodegradable molecular sieves could be a game-changer. These materials would break down naturally after their useful life, reducing waste and minimizing their environmental impact.
Frequently Asked Questions
What is gas separation using molecular sieves?
Gas separation with molecular sieves is a process that isolates specific gases from a mixture by selectively adsorbing one gas over others based on molecular size and polarity, resulting in high-purity gas streams.
How do molecular sieves separate gases?
Molecular sieves separate gases by adsorbing certain molecules onto their porous surface while allowing other molecules to pass through. The sieve’s pore size determines which gases are adsorbed and which are excluded.
What are common applications of gas separation with molecular sieves?
Common applications include oxygen production for medical use, nitrogen generation, hydrogen purification, and carbon dioxide removal in industries like healthcare, food, and petrochemicals.
What types of molecular sieves are used in gas separation?
Molecular sieves such as 5A, 13X, and MSOX are commonly used for gas separation. Each type has specific pore sizes and adsorption characteristics suited to different gases.
Can molecular sieves separate oxygen and nitrogen?
Yes, molecular sieves like 5A can effectively separate oxygen and nitrogen by adsorbing nitrogen and allowing an oxygen-rich stream to pass through, often used in oxygen concentrators.
How are molecular sieves used in hydrogen purification?
In hydrogen purification, molecular sieves adsorb impurities like nitrogen and carbon monoxide, leaving behind a purified hydrogen stream, crucial for fuel cell and chemical industries.
What is the role of molecular sieves in nitrogen generation?
Molecular sieves selectively adsorb oxygen from air, resulting in a nitrogen-rich output. This process is commonly used in food packaging and metal treatment industries.
How do molecular sieves help in carbon dioxide removal?
Molecular sieves like 13X can selectively adsorb carbon dioxide from gas mixtures, which is beneficial in applications like natural gas processing and air quality control.
What industries benefit most from gas separation using molecular sieves?
Industries such as healthcare, petrochemicals, food and beverage, environmental control, and manufacturing benefit significantly from gas separation processes.
Why are molecular sieves preferred over other gas separation methods?
Molecular sieves are preferred for their high selectivity, efficiency, and reusability. They also require less energy than cryogenic separation methods, making them cost-effective for on-site gas production.
How does gas purity affect industrial applications?
High-purity gases are essential in many applications, such as medical oxygen, food-grade nitrogen, and clean hydrogen for fuel cells. Purity affects product quality, safety, and operational efficiency.
What are the environmental benefits of using molecular sieves for gas separation?
Molecular sieves are reusable and energy-efficient, reducing waste and emissions compared to traditional separation methods, supporting more sustainable industrial practices.
Can molecular sieves be regenerated after gas separation?
Yes, molecular sieves can be regenerated by heating or applying a vacuum to release adsorbed gases, restoring their adsorption capacity for continued use.
What factors influence the efficiency of gas separation?
Factors include molecular sieve type, pore size, operating pressure, temperature, and the specific gas mixture composition, all impacting separation efficiency.
What is Pressure Swing Adsorption (PSA), and how does it relate to gas separation?
PSA is a process that uses molecular sieves to separate gases by varying pressure. It’s commonly used for oxygen and nitrogen generation, taking advantage of the selective adsorption properties of sieves.
How do molecular sieves compare with membrane-based gas separation?
Molecular sieves generally offer higher selectivity and can handle a broader range of gases, while membrane-based methods are often limited in purity levels and applicable gas types.
What safety precautions are required for gas separation with molecular sieves?
Safety measures include ensuring proper ventilation, monitoring pressure and temperature, and adhering to equipment and material handling guidelines specific to the gases involved.
Can molecular sieves be used for air purification in indoor environments?
Yes, molecular sieves can adsorb contaminants such as CO₂ and VOCs, improving indoor air quality in industrial settings and other controlled environments.
How is gas separation with molecular sieves used in food packaging?
In food packaging, molecular sieves help generate nitrogen-rich atmospheres by adsorbing oxygen, which slows down oxidation and extends product shelf life.
Where can I learn more about molecular sieve processes and applications?
For more information on molecular sieve processes and their industrial applications, visit our page on Key Molecular Sieve Processes.
Conclusion
Molecular sieves offer remarkable advantages for gas separation and purification across industries, thanks to their unique properties like selective adsorption and efficient regeneration. Compared to other adsorbents such as activated carbon, silica gel, and alumina, molecular sieves provide superior selectivity and flexibility.
With specialized types like Molecular Sieves 3A, Molecular Sieves 4A, Molecular Sieves 5A, and the versatile Molecular Sieves 13X, industries can target applications ranging from drying polar liquids to removing contaminants from natural gas. Molecular sieves also play a vital role in fields like green energy production and oxygen concentration using PSA technology, contributing to sustainability and efficiency.
For businesses looking to maximize efficiency and quality, understanding the properties and types of molecular sieves is essential. Explore our Comprehensive Guide to Molecular Sieves to gain insights into their applications across various industries and see how they can transform your processes for better performance. For more in-depth research on molecular sieves in industrial applications, visit this detailed study on ScienceDirect.
.