The Science Behind PSA: How Pressure Swing Adsorption Powers Our Industries
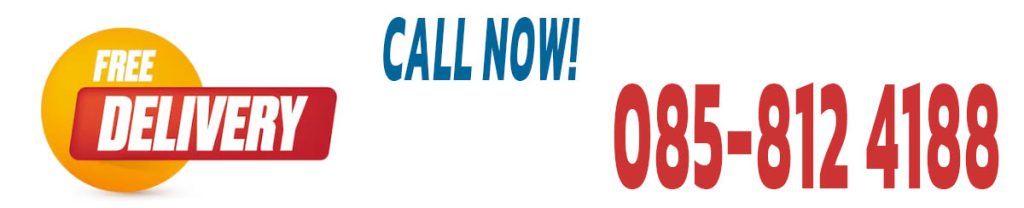
Key Topic | Summary |
---|---|
Pressure Swing Adsorption (PSA) | PSA is a gas separation method that uses adsorbents and fluctuating pressure to selectively trap gases. |
Adsorption and Desorption | Key mechanisms in PSA, where gases stick to or release from adsorbent materials. |
Applications in Industries | Widely used in medical oxygen production, food packaging, and chemical processes. |
Types of Filters Used | Includes molecular sieves, activated alumina, and silica gel for various purification needs. |
Benefits of PSA Technology | Cost-effective, energy-efficient, modular, and scalable for various uses. |
Table Of Contents
“PSA technology has been a breakthrough in simplifying gas separation while ensuring purity and efficiency.”
Introduction
Have you ever wondered how industries produce pure oxygen or nitrogen on demand? The answer lies in a fascinating technology called Pressure Swing Adsorption (PSA). Whether you need pure oxygen for hospitals, nitrogen to package food, or purified hydrogen for fuel cells, PSA has become an essential technology powering multiple industries.
Pressure Swing Adsorption is a versatile gas separation method that relies on the principles of adsorption and desorption to purify gases. Today, we’ll dive into the science behind PSA, exploring how it works, why it’s used, and the significant role it plays across industries. Along the way, I’ll share some real-life stories to make these concepts come alive—like how PSA helped save lives during the COVID-19 pandemic by supplying crucial medical oxygen. So let’s embark on this engaging journey into PSA technology and uncover how it shapes our world.
What is Pressure Swing Adsorption?
Think of Pressure Swing Adsorption as a process that acts like a selective sponge, absorbing the gas you want to keep and letting the rest pass by. Essentially, PSA technology utilizes specific adsorbent materials—like molecular sieves, activated alumina, and silica gel—to selectively trap gases from a mixture.
Pressure Swing Adsorption
Property | Description |
Method | Uses fluctuating pressure to separate gases through adsorption. |
Adsorbent Types | Molecular sieves, activated alumina, silica gel, activated carbon. |
Applications | Medical oxygen, nitrogen packaging, industrial gas purification. |
Key Mechanism | Adsorption at high pressure and desorption at low pressure. |
Adsorption is the process where certain molecules “stick” to the surface of adsorbents. During PSA, a mixture of gases passes through an adsorbent bed, which captures the target molecules (e.g., nitrogen or oxygen). Desorption is the reverse process, where reducing pressure allows these trapped gases to be released and collected. Just like squeezing a wet sponge to release water, desorption is what regenerates the adsorbent for reuse.
By carefully cycling between high and low pressures, PSA effectively separates the gases. It sounds simple, but this technology is crucial for purifying and generating high-quality industrial gases efficiently.
How Does PSA Work?
To understand how PSA works, imagine walking through a hallway filled with different doors, each labeled with a gas name—only certain gases are allowed through specific doors. The adsorbent materials inside a PSA unit serve as these “doors,” opening and closing based on the molecular properties of the gases.
Step-by-Step Process
- Adsorption: Compressed air enters the PSA unit, which contains a chamber filled with adsorbent materials like zeolite molecular sieves. These sieves trap certain gas molecules while allowing others to pass.
- Separation: The adsorbents act like guards, holding onto molecules with higher adsorption affinity (e.g., nitrogen) while letting the desired gas (e.g., oxygen) continue through the system.
- Desorption and Regeneration: When pressure is reduced, the trapped molecules are released, regenerating the adsorbent bed for the next cycle.
The adsorbent materials play a critical role in the efficiency of the PSA system. Activated alumina, molecular sieves, and silica gel each have unique properties that make them suitable for separating specific gases or removing impurities.
The alternating pressure—swinging from high to low—is what makes this method so effective for gas purification, and it’s the reason behind the name “Pressure Swing Adsorption.”
Step | Description |
Adsorption | High pressure causes adsorbent beds to trap gases. |
Separation | Adsorbent holds onto target gas molecules like nitrogen. |
Desorption and Regeneration | Lower pressure releases trapped gases, regenerating the adsorbent. |
Types of Filters and Adsorbents Used in PSA
The magic of PSA lies not just in pressure, but in the specialized filters and materials that make gas separation possible. Below is a brief summary of each filter type to help readers of all backgrounds easily understand their roles. Each adsorbent material is chosen for a particular purpose, depending on the type of gas being purified.
Activated Alumina
Activated alumina is often used to remove water vapor from gases. It acts as a drying agent, ensuring the gas entering the system is free from moisture. This pre-treatment step is essential for maintaining the performance of the primary adsorbent beds. See also our previous post: Activated Alumina Gas Purification: Effective Solutions for Industrial Gases like Hydrogen, Nitrogen, and Natural Gas.
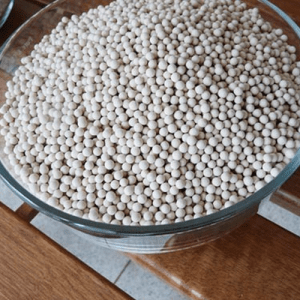
Adsorbent Type | Primary Function |
Activated Alumina | Water vapor removal, pre-treatment drying. |
Molecular Sieves | Separation of gases based on molecular size. |
Silica Gel | Residual moisture control, final purification. |
Activated Carbon | Removal of contaminants like hydrocarbons. |
See also our Comprehensive Guide to Activated Alumina
Molecular Sieve Filters
Molecular sieves, particularly zeolite-based ones, are the workhorses of PSA technology. They selectively trap gas molecules based on their size and shape, making them perfect for separating nitrogen from oxygen. These filters are highly effective for industrial gas separation and purification.
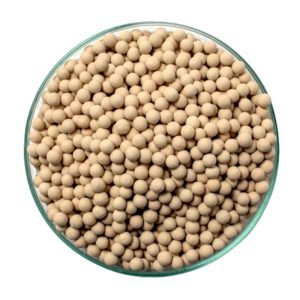
For more information about molecular sieves and their various applications, check out our previous post on Exploring the many uses of Molecular Sieves in various industries.
See also our Comprehensive Guide to Molecular Sieves
Silica Gel Adsorption
Silica gel helps manage residual moisture and ensures that the final product is dry. It can be used in both the pre-treatment and the final stages, adding an extra layer of purification. See our previous post: Choosing the Right Desiccant for Compressed Air Systems: A Comparison of Activated Alumina, Silica Gel, and Molecular Sieves
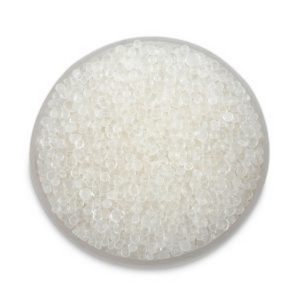
See also our Comprehensive Guide to Silica Gel
Activated Carbon in PSA
In some systems, activated carbon is also used to remove contaminants like hydrocarbons, ensuring the purity of the final gas product. See our previous post: Comparing CO2 Adsorption and N2 Adsorption on Activated Carbon, Alumina, and Zeolites.
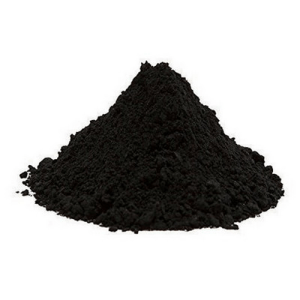
Each of these filters plays a key role in the PSA process, contributing to the overall efficiency and quality of gas production.
See also our Comprehensive Guide to Activated Carbon
Applications of PSA Technology
From hospitals to high-tech manufacturing, PSA technology powers many aspects of our everyday lives. Let me tell you a quick story for each application to show just how impactful PSA can be.
Medical Applications
During the COVID-19 pandemic, hospitals faced critical shortages of medical oxygen. PSA-based oxygen concentrators played a heroic role, providing life-saving oxygen to patients on-site when bottled supplies ran short. This technology quite literally saved lives when demand was at its highest.
One of the most significant uses of PSA is in producing oxygen for medical purposes. During the COVID-19 pandemic, PSA oxygen concentrators became lifesaving tools, delivering high-purity oxygen to patients in need. The ability to produce medical-grade oxygen on-site, without relying on transportation, made a difference in countless emergency situations.
Enhancing Medical Oxygen Production with Molecular Sieves
In PSA oxygen concentrators, molecular sieves are essential for achieving high oxygen purity by adsorbing nitrogen efficiently. These sieves help maintain the medical-grade oxygen standards required in healthcare settings, directly impacting patient care. For a closer look at the specialized sieves used in medical oxygen production, visit our detailed article on Molecular Sieves for Medical Oxygen Production.
Food Industry
Imagine opening a bag of your favorite potato chips, only to find they’re stale. Nitrogen purification using PSA helps prevent this by displacing oxygen in packaging, keeping snacks crisp and fresh for much longer. It’s one of the reasons why your chips stay perfectly crunchy!
Nitrogen is used extensively in food packaging to keep products fresh, and PSA technology is a primary method for nitrogen purification. By displacing oxygen in the packaging, nitrogen helps prolong the shelf life of perishable items like chips, coffee, and baked goods.
Industrial Gas Production
Breweries, for example, require a constant supply of nitrogen to purge tanks and maintain quality. PSA technology ensures these industries have high-purity nitrogen at an affordable cost, making sure your favorite craft beer is brewed just right, without unwanted oxidation. Its applications are diverse, with each playing a crucial role in ensuring the availability of high-purity gases.
Industry | PSA Application |
Medical | Oxygen production for hospitals and concentrators. |
Food Packaging | Nitrogen purification for displacing oxygen. |
Chemical | Purifying hydrogen, nitrogen, and other industrial gases. |
In the chemical industry, PSA is used for purifying hydrogen, nitrogen, and other gases that are essential for production. By using zeolite molecular sieves, industries can achieve high levels of purity at a fraction of the cost compared to traditional gas separation methods.
Think about breweries that need a constant supply of nitrogen to purge tanks or pharmaceutical plants requiring oxygen for chemical reactions. PSA technology offers the scalability and efficiency needed to meet these varied demands.
Chemical Industry: Purifying gases like hydrogen and nitrogen.
Medical Applications: Producing high-purity oxygen for hospitals.
Food Industry: Nitrogen gas helps prevent food spoilage.
Why is PSA Technology So Widely Used?
What makes PSA such a game-changer compared to other gas purification technologies? Let’s look at some of the reasons PSA is favored in so many industries.
Benefits Over Alternatives
- Cost-Effective: PSA units are energy-efficient and have lower operational costs compared to cryogenic gas separation.
- Continuous Operation: Unlike batch processes, PSA systems can run continuously, ensuring an uninterrupted supply of gases.
- Modularity and Scalability: PSA systems are highly adaptable. They can be scaled up or down depending on the quantity and purity of gas required.
Challenges
PSA isn’t without its challenges. The primary issue is sensitivity to impurities—if the incoming air isn’t adequately pre-treated, contaminants can degrade the adsorbent material and reduce efficiency. Clean, dry air is a must for PSA to operate optimally.
A Real-Life Story: PSA in Action
Let me share a story of how PSA saved the day for a local hospital during an oxygen supply shortage. With surging demand, traditional supply chains couldn’t keep up, and deliveries of bottled oxygen were running late. The hospital brought in PSA-based oxygen concentrators, allowing them to produce oxygen on-site without depending on dwindling external supplies. This quick adaptation not only helped meet patient needs but also demonstrated the resilience and scalability of PSA technology in critical times.
PSA Filters: How to Choose the Right Adsorbent
Selecting the right adsorbent for PSA depends on what gas you need to separate. Consider using the following simple checklist to help you decide:
- Gas Type: What gas are you trying to separate (e.g., nitrogen, oxygen)?
- Purity Requirements: How pure does the gas need to be for your application?
- Environmental Conditions: Are there any moisture or contaminant levels to consider?
For a visual guide, you could use a flowchart that starts with ‘Gas Type’ and branches out to the recommended adsorbent based on your answers. and how pure you need it to be. For instance, activated alumina is ideal for removing water vapor, while molecular sieves excel in separating nitrogen from oxy
Activated Alumina vs. Molecular Sieves
Activated alumina provides excellent pre-treatment, keeping moisture levels low and ensuring the adsorbents downstream don’t get clogged or degraded. On the other hand, molecular sieves are specialized for separating gases at a high purity level, such as nitrogen or hydrogen purification. See also: Choosing the Right Desiccant for Compressed Air Systems
Factors to Consider
When choosing between these materials, consider factors like gas type, purity requirements, and environmental conditions. Depending on your application, you may even need a combination of adsorbents to achieve optimal results. For further insights into activated alumina, you can refer to our product listing Activated Alumina 3-5mm (30kg/drum).
Future of PSA Technology
As industries grow more conscious of sustainability, PSA is evolving to meet the needs of a changing world. For example, companies like Air Liquide are making significant strides in applying PSA for hydrogen production, which is essential for clean energy initiatives. These efforts are helping drive the transition to renewable energy sources and reduce the carbon footprint of industrial operations. There are ongoing advancements aimed at improving adsorbent materials, making them more efficient and longer-lasting.
Advancements in PSA
One of the most exciting areas is hydrogen production for green energy. By increasing efficiency and reducing the energy required for pressure swings, PSA can contribute to cleaner, renewable energy solutions in the coming years. Additionally, PSA is being researched for use in carbon capture technologies, which could play a pivotal role in mitigating climate change. To explore more about how PSA operates efficiently, check out this article on Optimal startup operation of a pressure swing adsorption.
- Hydrogen Production: PSA is key in generating pure hydrogen for clean energy applications.
- Carbon Capture: Future PSA applications could help in mitigating emissions through carbon capture.
“While PSA is efficient, it requires extremely clean air to maintain its effectiveness over long-term use.”
Frequently Asked Questions
Pressure Swing Adsorption (PSA) is a versatile and efficient technology, but it can raise a lot of questions for those new to it. Below, we answer some of the most common questions about how PSA works, its applications, and why it’s favored across industries.
What is Pressure Swing Adsorption (PSA)?
Pressure Swing Adsorption is a gas separation technique that uses adsorbent materials to selectively trap gases at high pressure and release them at low pressure, making it ideal for industrial gas purification.
How does PSA work in gas separation?
PSA works by cycling between high and low pressures, allowing adsorbent materials to selectively capture certain gas molecules during adsorption and release them during desorption.
What are the main applications of PSA technology?
PSA is widely used in medical oxygen production, nitrogen purification for food packaging, and industrial gas production for chemical processes.
Why is PSA technology preferred for oxygen concentrators?
PSA is preferred because it allows on-site production of high-purity oxygen, which is essential for medical applications and emergency situations.
What role does activated alumina play in PSA?
Activated alumina is used to remove moisture from gases during pre-treatment, ensuring that the adsorbent materials perform optimally.
How does a molecular sieve filter work in PSA?
Molecular sieve filters, such as zeolite, selectively trap gas molecules based on their size, effectively separating gases like nitrogen from oxygen.
What gases can be separated using PSA?
PSA can be used to separate various gases, including oxygen, nitrogen, hydrogen, and other industrial gases.
What industries benefit most from PSA technology?
Industries such as healthcare (for oxygen), food packaging (for nitrogen), and chemical manufacturing (for hydrogen and other gases) benefit significantly from PSA technology.
How does silica gel assist in PSA technology?
Silica gel helps manage residual moisture, ensuring that the final gas product is dry and suitable for further use.
What is the difference between adsorption and desorption?
Adsorption involves gas molecules sticking to the adsorbent surface, while desorption is the process of releasing those molecules by reducing pressure.
Is PSA energy efficient compared to other gas purification methods?
Yes, PSA is considered more energy-efficient compared to cryogenic methods, particularly for smaller-scale applications.
Can PSA systems be scaled for different industrial needs?
Yes, PSA systems are modular and scalable, making them adaptable for different gas quantities and purity levels.
What is nitrogen purification and why is it important?
Nitrogen purification involves removing oxygen and other impurities to ensure nitrogen is suitable for use in food packaging, where it prevents spoilage.
What is the significance of activated carbon in PSA systems?
Activated carbon is used to remove contaminants like hydrocarbons from the gas stream, ensuring high purity in the final product.
How does PSA compare to gas filtration methods like membranes?
PSA is generally more cost-effective for producing high-purity gases, while membrane methods may be more suitable for partial separation.
What are zeolite molecular sieves used for in PSA?
Zeolite molecular sieves are primarily used for separating nitrogen from air, allowing for efficient production of high-purity oxygen.
Why is clean, dry air important in PSA?
Contaminants and moisture can degrade the adsorbent materials in PSA, reducing efficiency, which is why pre-treatment like activated alumina is crucial.
What advancements are being made in PSA technology?
Advancements include improving adsorbent materials to make them more efficient and exploring PSA’s role in hydrogen production and carbon capture.
What is the gas drying process in PSA?
The gas drying process involves removing moisture from the gas mixture using adsorbents like activated alumina or silica gel to ensure optimal performance.
How does PSA contribute to industrial gas production?
PSA provides a cost-effective way to produce gases like oxygen, nitrogen, and hydrogen, which are essential for various industrial applications.
Conclusion
Pressure Swing Adsorption might sound like a complex process, but at its core, it’s all about making our air cleaner, our products fresher, and our energy greener. For more detailed insights into the adsorbents used in PSA, check out our cornerstone pages: A comprehensive guide to Activated Alumina, A Comprehensive Guide to Molecular Sieves, and A Comprehensive Guide to Activated Carbon. PSA technology is an indispensable tool across industries, from medical oxygen production to food preservation and energy sustainability.
If you’re interested in learning more about adsorbents for PSA or finding the right filter for your needs, feel free to visit our product categories for Activated Alumina, Molecular Sieve, Silica Gel, Bleaching Earth, or Activated Carbon. For anyone curious about how PSA technology could fit into your industrial processes, I’d love to hear your thoughts or questions.
Disclaimer
This post is intended for educational purposes only. Please consult an industry professional for specific guidance related to PSA technology and its applications in your particular field.
ขอบคุณที่ใช้เวลาอ่านบทความของเราเกี่ยวกับการป้องกันความชื้น ทางเราหวังว่าท่านจะได้รับข้อมูลที่มีคุณค่าและเป็นประโยชน์ ทางเรายินดีให้บริการการปรึกษาฟรีเพื่อพูดคุยเกี่ยวกับความต้องการของท่านและให้คำแนะนำเกี่ยวกับวิธีการป้องกันความชื้นที่กำหนดเฉพาะสำหรับคุณ โปรดติดต่อเราที่ 0858124188 เพื่อนัดหมายการปรึกษาหรือเยี่ยมชมร้านค้าของเราเพื่อค้นหาผลิตภัณฑ์ที่ช่วยป้องกันสินค้าของคุณจากความเสียหายจากความชื้น ทางเราหวังว่าจะได้รับข่าวสารจากท่านเร็วๆนี้