Activated Alumina for Sulfur Removal in Refining Processes
Topic | Summary |
---|---|
Activated Alumina | A powerful adsorbent used in refining processes to remove sulfur compounds efficiently. |
Sulfur Compounds in Refining | Sulfur is present in crude oil and natural gas, causing equipment corrosion and environmental issues. |
Sulfur Adsorption | Activated Alumina effectively adsorbs sulfur molecules, ensuring cleaner hydrocarbon streams. |
Applications in Refining | Activated Alumina is widely used in oil refining, natural gas purification, and desulfurization units. |
Advantages | High efficiency, durability, cost-effectiveness, and stability under harsh conditions. |
Table Of Contents
Activated Alumina removes sulfur compounds through adsorption, where sulfur molecules adhere to its high surface area, ensuring cleaner hydrocarbon streams and protecting refining equipment from sulfur-induced corrosion.
Activated Alumina for Sulfur Removal in Refining Processes
When it comes to refining processes, controlling sulfur content is one of the biggest challenges faced by the industry, and Activated Alumina for sulfur removal offers a powerful solution. Sulfur is naturally present in crude oil and natural gas, and if not removed, it can lead to significant environmental and operational issues. Activated Alumina for sulfur removal not only ensures compliance with stringent regulations but also helps in producing higher-quality end products. In this post, we’ll explore how Activated Alumina for sulfur removal has become the go-to material for sulfur removal, offering an efficient and reliable way to tackle this pervasive problem in the refining industry.
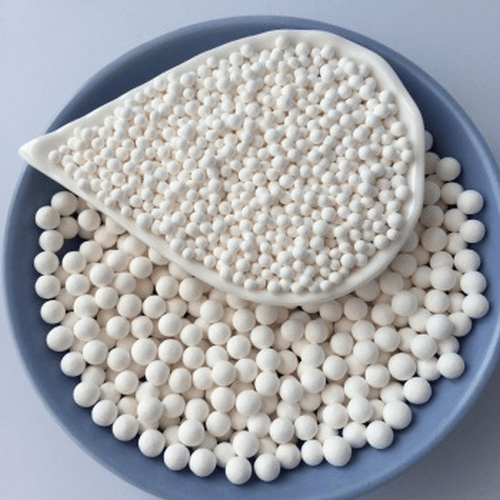
Activated Alumina for sulfur removal, with its remarkable adsorptive properties, has carved a niche in the oil and gas sector, particularly for sulfur removal. From natural gas purification to hydrocarbon processing, this versatile adsorbent continues to enhance refining operations. With an increasing need to meet environmental standards and improve product quality, the role of Activated Alumina for sulfur removal in desulfurization processes cannot be overstated.
Parameter | Description |
---|---|
Material | Activated Alumina |
Main Use | Sulfur removal in oil refining and natural gas purification |
Adsorptive Capacity | High surface area and pore volume for effective sulfur adsorption |
Key Sulfur Compounds Removed | Hydrogen sulfide (H2S), mercaptans, and other sulfur compounds |
Operational Benefits | Reduced emissions, equipment protection, compliance with environmental standards |
Industries | Oil & Gas, Hydrocarbon Processing, Refining Operations |
Understanding Sulfur in Refining Operations
Sulfur compounds in oil and gas refining can wreak havoc if not properly managed. When crude oil or natural gas is processed, sulfur-containing compounds such as hydrogen sulfide (H2S) and mercaptans emerge as significant challenges. These compounds, if left untreated, not only cause corrosion to equipment but also result in toxic emissions that can have severe environmental consequences. In a world where sustainability and operational efficiency are becoming increasingly vital, finding a reliable solution to control sulfur levels has become imperative.
Moreover, regulatory bodies like the Environmental Protection Agency (EPA) enforce stringent sulfur emission limits for refineries, making sulfur control a critical part of any refining operation. Without proper desulfurization processes, refiners risk costly fines, operational downtime, and significant environmental damage. This is where Activated Alumina for sulfur removal steps in, offering a high-performance solution for sulfur removal in both oil refining and natural gas purification processes.
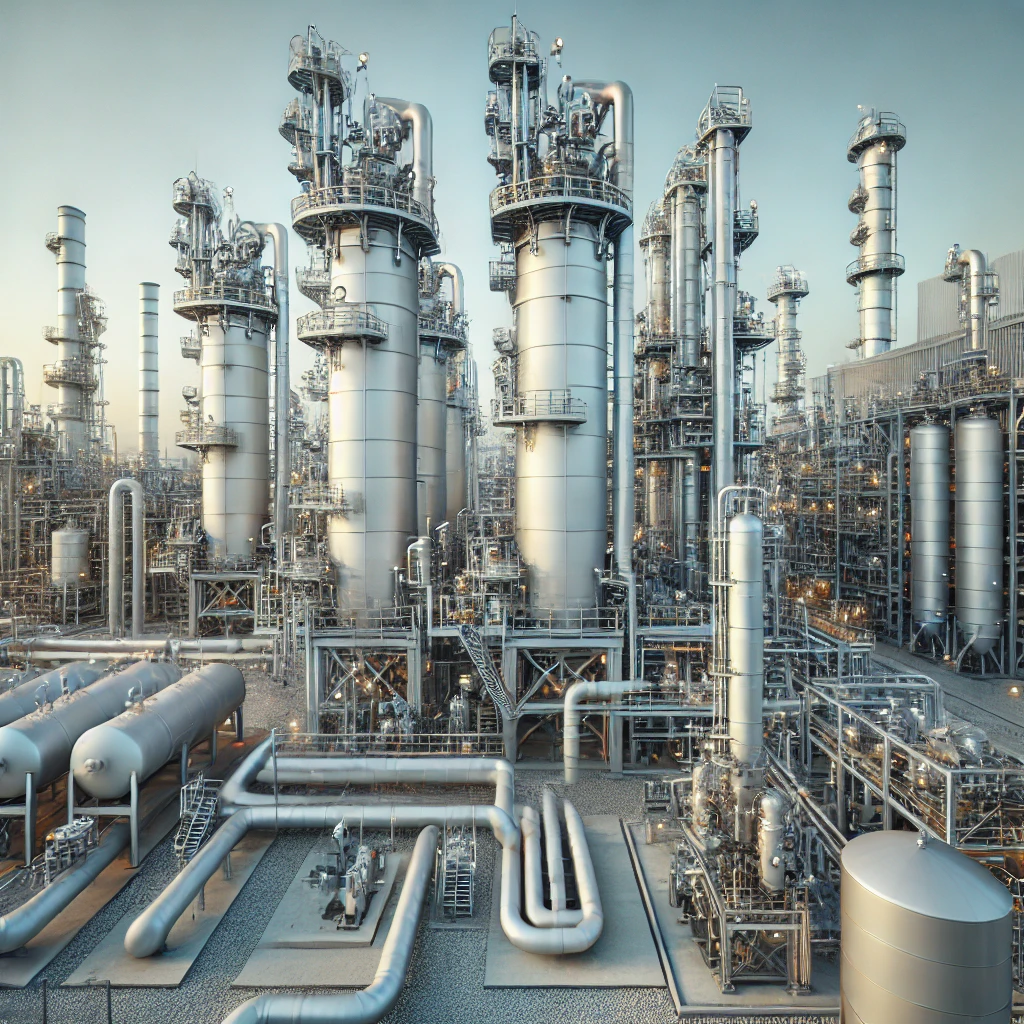
One of the biggest challenges I’ve encountered in sulfur removal during refining operations was dealing with the unpredictability of sulfur concentrations in different crude oil feedstocks. Sulfur compounds like hydrogen sulfide (H2S) and mercaptans not only corrode equipment but also impair catalyst performance, reducing overall efficiency. We often saw significant operational disruptions due to this, leading to increased maintenance costs and downtime. Activated Alumina for sulfur removal proved to be a game changer because of its consistent adsorption performance, regardless of fluctuations in sulfur content. Its ability to capture and retain sulfur molecules effectively minimized equipment wear and tear and improved the stability of downstream processes, making it a reliable solution in our refining operations.
What is Activated Alumina?
Activated Alumina for sulfur removal is a highly porous, chemically inert material that serves as an exceptional adsorbent. Composed primarily of aluminum oxide (Al2O3), this material is processed to create a vast surface area with numerous pores. These pores make Activated Alumina for sulfur removal highly efficient in adsorbing a wide range of compounds, particularly sulfur. Its chemical stability, combined with its ability to withstand high temperatures and pressures, makes it a perfect choice for industrial refining applications.
The production process of Activated Alumina for sulfur removal involves careful heating and activation to maximize its adsorptive capacity. In sulfur removal applications, its role is clear—sulfur compounds like H2S and mercaptans are trapped within the pores, ensuring that only purified hydrocarbons pass through the system. This makes it a go-to solution for sulfur control, particularly in refining processes that require stringent sulfur limits. With its high surface area and excellent mechanical strength, Activated Alumina for sulfur removal outperforms many other adsorbents in this field.
Key Properties of Activated Alumina
Property | Details |
---|---|
Chemical Composition | Aluminum Oxide (Al2O3) |
Surface Area | 300-360 m²/g |
Pore Volume | 0.38-0.45 cm³/g |
Crush Strength | ≥150 N (3-5 mm) |
Static Water Adsorption | 16-18% (RH 60%, 25°C) |
Bulk Density | 0.63-0.75 g/ml |
Mechanism of Sulfur Removal Using Activated Alumina
Activated Alumina for sulfur removal removes sulfur compounds through a process of adsorption, where sulfur molecules adhere to its surface. In this adsorption process, sulfur compounds such as hydrogen sulfide and mercaptans are captured as the gas or liquid passes through beds of Activated Alumina for sulfur removal. Due to its high surface area, Activated Alumina for sulfur removal can adsorb significant quantities of sulfur, making it highly effective for desulfurization.
What makes Activated Alumina for sulfur removal particularly suited for sulfur adsorption is its ability to maintain efficiency under harsh refining conditions. Whether dealing with high temperatures, pressures, or corrosive environments, Activated Alumina for sulfur removal retains its structural integrity, ensuring reliable sulfur removal. Desulfurization units in oil and gas refineries often rely on Activated Alumina for sulfur removal to capture and control sulfur emissions. The adsorbent can be regenerated, extending its lifecycle and maintaining performance over long operational periods.
Sulfur Adsorption Mechanism of Activated Alumina
Step | Description |
---|---|
1. Gas/Liquid Flow | Hydrocarbon streams containing sulfur compounds flow through the alumina bed |
2. Adsorption | Sulfur molecules adhere to the porous surface of the Activated Alumina |
3. Retention | Sulfur remains trapped within the pores, ensuring a cleaner output stream |
4. Regeneration | Spent alumina can be regenerated for continuous sulfur removal |
Applications of Activated Alumina in Refining
Activated Alumina for sulfur removal finds applications in a variety of refining processes, especially where sulfur control is critical. In oil refining, desulfurization units utilize Activated Alumina for sulfur removal to capture sulfur compounds before they can damage processing equipment or be emitted into the atmosphere. Its role in sulfur recovery units ensures that refiners can recover valuable sulfur while maintaining compliance with environmental regulations.
In natural gas purification, Activated Alumina for sulfur removal plays a similar role. Gas streams often contain significant amounts of sulfur compounds, which must be removed before the gas is processed further or used commercially. Activated Alumina for sulfur removal efficiently adsorbs these compounds, allowing for cleaner gas streams that meet regulatory standards. Additionally, its role in hydrocarbon treatment and gas drying enhances the overall refining process, improving both efficiency and product quality.
Activated Alumina Applications in Refining
Application | Role of Activated Alumina |
---|---|
Oil Refining | Captures sulfur compounds in desulfurization units |
Natural Gas Purification | Removes sulfur and moisture from gas streams |
Hydrocarbon Processing | Used for gas drying, ensuring hydrocarbon streams are free of sulfur |
Sulfur Recovery Units | Helps recover sulfur from exhaust gases |
Case Study: Success Story in Sulfur Control
Let’s take a look at how one refinery successfully used Activated Alumina for sulfur removal to meet strict environmental regulations. This particular refinery, located in Southeast Asia, faced mounting pressure to reduce sulfur emissions due to newly imposed government regulations. Using Activated Alumina for sulfur removal, the refinery was able to significantly reduce sulfur levels in its output streams, achieving compliance with the new sulfur limits within months.
Not only did this solution help the refinery avoid costly fines, but it also improved operational efficiency. The use of Activated Alumina for sulfur removal extended the life of critical refining equipment by preventing sulfur-induced corrosion, and the overall sulfur recovery rate increased. This success story highlights the real-world impact Activated Alumina for sulfur removal can have on refining operations, making it a cornerstone of modern desulfurization technologies.
A particular instance that comes to mind is when I was leading a refinery project in a region where new environmental regulations were introduced, limiting sulfur emissions. We had to quickly adapt our processes to meet these strict standards or face heavy fines. Implementing Activated Alumina for sulfur removal allowed us to reduce the sulfur content in our gas emissions by over 90%. The adsorbent was able to remove hydrogen sulfide efficiently, which was a key contributor to our emissions issues. This not only helped us comply with the new regulations but also improved the overall sustainability of our operations, allowing us to continue refining without the risk of costly shutdowns or environmental penalties.
Advantages of Using Activated Alumina for Sulfur Removal
Why choose Activated Alumina for sulfur removal? The advantages are clear. First, it offers high sulfur removal efficiency, capturing significant quantities of sulfur even in harsh industrial environments. This makes it one of the most effective adsorbents for desulfurization. Second, Activated Alumina for sulfur removal is known for its longevity and durability, even under the extreme pressures and temperatures commonly found in refining operations. This translates to reduced operational costs and improved efficiency over time.
Additionally, Activated Alumina for sulfur removal is highly cost-effective compared to other sulfur removal technologies. Its ability to be regenerated and reused means that refineries can get more value out of their investment. Moreover, its stability at high temperatures allows it to handle large volumes of hydrocarbons without losing performance. These factors make Activated Alumina for sulfur removal a top choice for refineries looking to implement or improve their sulfur control strategies.
Benefits of Activated Alumina for Sulfur Removal
Advantage | Description |
---|---|
High Sulfur Removal | Removes significant quantities of sulfur efficiently |
Durability | Withstands harsh refining conditions such as high temperatures and pressure |
Cost-Effective | Can be regenerated, lowering operational costs |
Environmental Compliance | Helps refineries meet sulfur emission standards |
From a technical standpoint, what sets Activated Alumina for sulfur removal apart is its exceptional surface area and mechanical strength, which allow it to adsorb a large volume of sulfur compounds without losing efficiency over time. In large-scale refining operations, where consistency and reliability are crucial, Activated Alumina maintains its performance even under extreme temperatures and pressures. Unlike other sulfur removal technologies that might require frequent replacement or regeneration, Activated Alumina offers a longer lifecycle and can be regenerated multiple times, making it a more cost-effective and durable option for long-term sulfur control. Its versatility across various refining environments, combined with its high adsorption capacity, makes it the superior choice in most large-scale operations.
Activated Alumina stands out due to its ability to withstand extreme operational conditions in refining, maintaining high sulfur removal efficiency while reducing costs through regeneration and reuse.
Frequently Asked Questions
What is Activated Alumina and how is it used in sulfur removal?
Activated Alumina is a porous, highly adsorbent material made from aluminum oxide. It is used in refining processes to remove sulfur compounds like hydrogen sulfide (H2S) and mercaptans by adsorbing these sulfur molecules onto its surface, ensuring cleaner gas and liquid streams.
Why is sulfur removal important in oil and gas refining?
Sulfur removal is essential in oil and gas refining to prevent corrosion of equipment, avoid catalyst poisoning, reduce toxic emissions, and comply with environmental regulations. High levels of sulfur in hydrocarbons can negatively affect both refining processes and the final product quality.
How does Activated Alumina work for sulfur removal in refining operations?
Activated Alumina works through a process called adsorption, where sulfur compounds adhere to its highly porous surface. As the gas or liquid passes through beds of Activated Alumina, sulfur is trapped, allowing purified hydrocarbons to continue through the refining process.
What are the key advantages of using Activated Alumina for sulfur removal?
Activated Alumina offers high efficiency in sulfur removal, durability under extreme conditions, and the ability to regenerate and reuse the material. Its high surface area and pore volume make it highly effective at adsorbing sulfur compounds.
Can Activated Alumina be used for sulfur control in both oil refining and natural gas purification?
Yes, Activated Alumina is widely used in both oil refining and natural gas purification. It adsorbs sulfur compounds from crude oil, natural gas, and other hydrocarbons, ensuring that the final product meets sulfur content regulations.
What types of sulfur compounds can Activated Alumina remove from hydrocarbons?
Activated Alumina is effective in removing a variety of sulfur compounds, including hydrogen sulfide (H2S), mercaptans, and sulfur oxides, which are commonly found in crude oil and natural gas.
How is Activated Alumina different from other adsorbents used for sulfur removal?
Compared to other adsorbents, Activated Alumina offers greater mechanical strength, a higher surface area, and better performance at elevated temperatures and pressures. It also has a longer lifespan and can be regenerated, making it more cost-effective in industrial refining applications.
How does sulfur removal using Activated Alumina benefit the environment?
Activated Alumina helps reduce sulfur emissions, which are harmful to the environment. By capturing sulfur compounds before they are released, refining operations can lower their environmental impact, reduce acid rain, and meet strict regulatory requirements.
Can Activated Alumina be regenerated after it’s used in sulfur removal?
Yes, Activated Alumina can be regenerated after sulfur adsorption. This regeneration process typically involves heating the material to release the adsorbed sulfur compounds, allowing the alumina to be reused multiple times, which makes it a cost-effective option in long-term operations.
What makes Activated Alumina an ideal adsorbent for sulfur control in industrial refining?
Activated Alumina is ideal due to its high adsorption capacity, stability under harsh conditions, and versatility in removing a range of sulfur compounds. Its ability to operate effectively in both high and low temperatures makes it suitable for a variety of refining environments.
How is Activated Alumina used in hydrocarbon processing for sulfur control?
In hydrocarbon processing, Activated Alumina is used to treat crude oil and natural gas streams. It adsorbs sulfur compounds before the hydrocarbons undergo further refining, ensuring that the process is cleaner and that equipment is protected from sulfur-induced corrosion.
Is Activated Alumina used in desulfurization technologies?
Yes, Activated Alumina plays a crucial role in desulfurization technologies, particularly in sulfur recovery units (SRUs) and gas sweetening processes. It adsorbs sulfur compounds and is part of the broader sulfur removal technology used in refineries.
How does Activated Alumina help with sulfur recovery in oil refineries?
In sulfur recovery units (SRUs), Activated Alumina helps capture sulfur compounds from hydrocarbon streams, which can then be processed and recovered as elemental sulfur. This recovered sulfur is often sold as a valuable by-product in industries like fertilizers and chemicals.
What impact does sulfur control have on refining operations?
Effective sulfur control using Activated Alumina improves refining operations by protecting equipment from corrosion, reducing downtime, and increasing the efficiency of catalysts. It also helps refineries meet environmental standards and maintain product quality.
Can Activated Alumina be used alongside other desulfurization methods in refining processes?
Yes, Activated Alumina can complement other desulfurization methods, such as hydrodesulfurization (HDS). By acting as a pre-treatment or post-treatment adsorbent, Activated Alumina enhances the overall sulfur removal efficiency in refining operations.
How is Activated Alumina incorporated into natural gas purification systems?
In natural gas purification, Activated Alumina is used to adsorb both sulfur compounds and moisture. It ensures that the gas is free from corrosive elements like H2S, allowing for cleaner combustion and less wear on downstream equipment.
What role does Activated Alumina play in sulfur adsorption during hydrocarbon processing?
During hydrocarbon processing, Activated Alumina adsorbs sulfur compounds from gas and liquid streams. This reduces the sulfur content, protecting refining equipment and ensuring that the processed hydrocarbons meet quality and environmental standards.
Are there specific grades of Activated Alumina for sulfur removal in different refining processes?
Yes, there are different grades of Activated Alumina, designed for specific sulfur removal applications. These grades may vary in pore size, surface area, and mechanical strength, depending on the requirements of the refining process.
How does Activated Alumina contribute to long-term operational efficiency in oil refineries?
Activated Alumina enhances long-term operational efficiency by reducing equipment corrosion, lowering maintenance costs, and increasing the lifespan of catalysts and refining units. Its ability to be regenerated also reduces material replacement costs.
What industries benefit most from using Activated Alumina for sulfur removal?
Industries such as oil and gas refining, petrochemical processing, and natural gas purification benefit significantly from using Activated Alumina for sulfur removal. These industries rely on efficient sulfur control to meet environmental standards and maintain product quality.
Conclusion
Activated Alumina for sulfur removal remains a cornerstone of modern refining operations, ensuring efficient sulfur control while safeguarding the environment. With its exceptional adsorptive properties, ability to perform under extreme conditions, and cost-effectiveness, it’s no wonder that refineries across the globe continue to rely on Activated Alumina for sulfur removal. In a world where environmental regulations are becoming stricter, and product quality is paramount, Activated Alumina for sulfur removal offers a proven solution that keeps refining processes running smoothly and sustainably.
To fully understand the versatility of activated alumina, we invite you to explore other applications of Activated Alumina in diverse industries. From gas purification and moisture control to catalytic processes, activated alumina plays a critical role in enhancing efficiency and ensuring quality across a range of industrial uses.
For those looking to improve their sulfur control capabilities, I recommend exploring our comprehensive range of Activated Alumina products. You can also learn more about choosing the right desiccant for your specific needs in my previous post Choosing the Right Desiccant for Compressed Air Systems or Activated Alumina Gas Purification: Effective Solutions for Industrial Gases like Hydrogen, Nitrogen, and Natural Gas.
For a deeper dive into desiccant technologies, refer to A Complete Guide to Activated Alumina Ready to upgrade your sulfur removal technology? Check out the Activated Alumina 3-5mm (30kg/drum) for more details.
See also: ScienceDirect: Adsorptive desulfurization by activated alumina
Disclaimer: The information provided in this post is based on current industry practices and is intended for educational purposes only. Please consult a professional for specific technical guidance.