Ceramic Balls 101: Understanding Their Types, Uses, and Benefits
Topic | Summary |
---|---|
Types of Ceramic Balls | Silicon Nitride, Alumina, Zirconia, and Silica offer distinct properties for varied uses. |
Properties | High hardness, heat resistance, corrosion resistance, low density, and electrical insulation. |
Applications | Used in bearings, grinding media, filtration systems, valves, and the chemical industry. |
Advantages and Challenges | Highly durable and lightweight but can be brittle and costly. |
Common Industries | Aerospace, automotive, oil & gas, chemical processing, and medical devices. |
Table Of Contents
Introduction
Ceramic balls are fascinating and versatile components that play a crucial role across a wide spectrum of industries. From high-performance bearings to precision grinding, ceramic balls offer unique properties that make them an excellent choice for many specialized applications. This introduction will help you understand the different types of ceramic balls, their specific uses, and why they are so beneficial. Let’s delve into the world of ceramic balls and explore their amazing properties.
Ceramic balls are made from industrial ceramic materials, which gives them exceptional qualities such as hardness, heat resistance, and corrosion resistance. Unlike steel balls, ceramic balls offer a level of chemical inertness that makes them perfect for environments where contamination must be minimized. The lightweight nature of ceramic materials also makes them easier to use in applications where reducing weight is a key consideration.
Types of Ceramic Balls
Ceramic balls come in a variety of types, each with its own unique benefits and suitable applications. Among the most popular types are Silicon Nitride (Si₃N₄), Alumina (Al₂O₃), Zirconia (ZrO₂), and Silica (SiO₂). Each material offers specific advantages.
Ceramic Balls
Type of Ceramic Ball | Key Properties | Common Applications |
Silicon Nitride | High strength, wear resistance | Aerospace, high-speed bearings |
Alumina | Corrosion resistance, thermal stability | Chemical industries, grinding media |
Zirconia | High fracture toughness, wear resistance | Mechanical shock environments, valves |
Silica | Chemical stability, moisture absorption | Desiccants, filtration systems |
Silicon Nitride Ceramic Balls
Silicon nitride ceramic balls are known for their high strength, wear resistance, and the ability to withstand high temperatures, making them suitable for high-performance applications in aerospace and defense. Their lightweight and durable nature also make them ideal for applications requiring high speed and minimal friction.
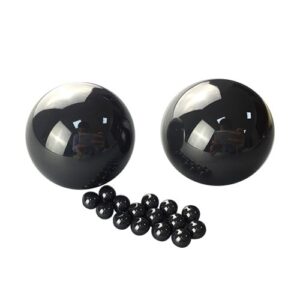
Alumina Ceramic Balls
Alumina Ceramic balls are prized for their excellent corrosion resistance and good thermal stability, making them highly useful in chemical industries. They are often used in environments where chemical inertness is crucial, as they do not react with the substances they come in contact with.
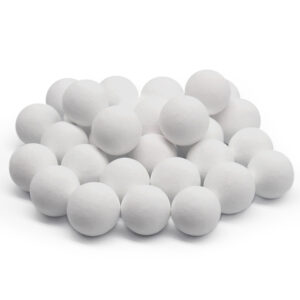
To learn more about specific industrial applications, check out our detailed article on Top Industrial Uses for Alumina Ceramic Balls.
Zirconia Ceramic Balls
Zirconia ceramic balls are characterized by their high fracture toughness and wear resistance, making them ideal for environments that require resistance to mechanical shock. Zirconia is heavier than other ceramics, providing extra strength where needed.
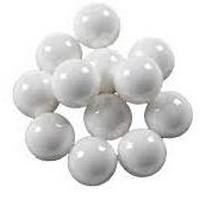
Silica Ceramic Balls
Silica ceramic balls, while not as robust in mechanical applications, are often used for their chemical stability and ability to absorb moisture, acting as desiccants in various setups. These different types cater to a wide range of uses, enabling ceramic balls to be employed in everything from precision bearings to filtration systems.
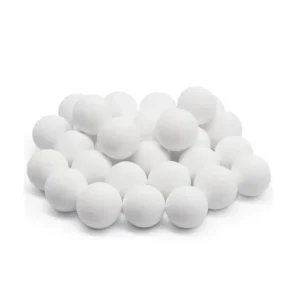
Properties of Ceramic Balls
The unique properties of ceramic balls set them apart from other materials.
Hardness
Hardness is one of their most significant characteristics; ceramic balls are incredibly hard, often surpassing the hardness of steel. This makes them exceptionally suitable for applications where they endure high wear and tear.
Heat Resistance
Their heat resistance allows them to perform effectively in high-temperature environments that would typically degrade other materials. This property is particularly advantageous in high-speed machinery and aerospace components.
Corrosion Resistance
Ceramic balls are also well-known for their corrosion resistance. This resistance to acids, alkalis, and salts makes them suitable for use in harsh and corrosive environments, such as chemical processing plants.
Low Density
Their low density further enhances their utility by reducing the overall weight of the machinery in which they are employed. This is especially beneficial in aerospace applications, where weight reduction is key.
Electrical Insulation
Finally, ceramic balls exhibit electrical insulation properties, making them indispensable for situations where electrical conductivity is undesirable, such as in electronic components.
Properties of Ceramic Balls
Property | Description | Benefits |
Hardness | Extremely hard, surpassing steel | High wear resistance, long lifespan |
Heat Resistance | Capable of withstanding very high temperatures | Suitable for high-temperature environments |
Corrosion Resistance | Resistant to acids, alkalis, and salts | Ideal for harsh environments |
Low Density | Lightweight compared to metal | Reduces weight of machinery |
Electrical Insulation | Non-conductive | Useful in electronic components |
Applications of Ceramic Balls
Ceramic balls are utilized in a wide array of industrial applications due to their distinct properties.
Bearings
One common use is in bearings. For example, silicon nitride ceramic balls are frequently used in high-speed bearings because of their lightweight nature, high strength, and reduced friction compared to steel balls. These attributes are particularly advantageous in demanding environments, such as the aerospace and automotive industries, where durability and weight reduction are essential.
Grinding Media
Another important use of ceramic balls is as grinding media. Ceramic grinding media, made from durable materials like alumina or zirconia, are essential for blending materials such as chemicals, ores, and ceramic powders. The inherent hardness of ceramic materials allows for efficient grinding without contamination, which is crucial in pharmaceutical or food industries.
Filtration Systems
Additionally, ceramic filtration balls are widely used in filtration systems, often serving as packing material in chemical processing. Their chemical inertness and ability to withstand harsh conditions make them ideal for these applications.
Valves and Pumps
Ceramic balls are also employed in valves and pumps, especially in the chemical and petrochemical industries. Their hardness and resistance to corrosion provide reliability and extend the life of these components.
Desiccant Applications
In some cases, silica-based ceramic balls are used as desiccants due to their ability to absorb moisture. This application is especially valuable in industries like electronics and pharmaceuticals, where moisture control is critical.
Applications of Ceramic Balls
Application | Industry | Benefits Provided |
Bearings | Aerospace, Automotive | High speed, reduced friction, lightweight |
Grinding Media | Chemical, Food | Efficient grinding, contamination-free |
Filtration Systems | Chemical Processing | Chemical inertness, durable in harsh environments |
Valves and Pumps | Petrochemical | Hardness, extended lifespan, corrosion resistance |
Desiccant | Electronics, Pharma | Moisture absorption, maintains product integrity |
Advantages and Challenges
Ceramic balls offer several distinct advantages over traditional materials like steel.
Advantages
One of their most significant advantages is their durability. Ceramic balls tend to have a much longer lifespan compared to their steel counterparts, primarily due to their resistance to wear. This makes them a cost-effective choice in the long run for many industrial applications.
Their high-temperature performance makes ceramic balls an obvious choice in environments with extreme heat, such as furnaces or aerospace components. Their lightweight nature is also a big plus, especially in applications where weight savings translate into better performance or fuel efficiency.
Challenges
However, ceramic balls also come with some challenges. Their brittleness is one of the major drawbacks. While ceramic balls are incredibly hard, they can be prone to cracking or breaking under sudden impacts or excessive pressure. This characteristic makes them less suitable for environments that involve heavy shocks or unpredictable loads.
Additionally, the cost of manufacturing ceramic balls can be higher compared to traditional steel balls, which may be a limiting factor for some industries that are cost-sensitive.
Common Industries Using Ceramic Balls
Aerospace and defense industries are major users of ceramic balls, particularly in high-stress components where durability and weight reduction are crucial. Ceramic ball bearings help improve the efficiency of aerospace machinery, providing reliable performance even in extreme conditions.
The automotive industry also finds great use for ceramic balls, especially in high-speed turbochargers and electric motors, where their heat resistance and lightweight properties help enhance performance.
In the oil & gas industry, ceramic balls are commonly used in pumps and valves where their corrosion resistance is a significant advantage. They help extend the life of the equipment, minimizing maintenance costs.
Similarly, in chemical processing applications, ceramic balls are used due to their chemical inertness, which ensures that they do not react with the processed materials, thus preserving the purity and quality of the chemicals.
Additionally, in medical devices, ceramic balls are used in precision devices that require non-reactive, high-performance components, making them ideal for medical environments.
Why Ceramic Balls Are a Game-Changer
The benefits of ceramic balls in industries like aerospace, automotive, and oil & gas cannot be overstated. Their unique combination of durability, lightweight properties, and resistance to heat and corrosion makes them a game-changing technology for high-performance applications. Whether it’s for improving fuel efficiency in aircraft engines or creating more efficient grinding systems in chemical manufacturing, ceramic balls offer distinct advantages that help industries push the boundaries of what’s possible.
Another interesting aspect is how ceramic balls are used as ceramic ball desiccants. Silica-based ceramic balls can absorb significant amounts of moisture, making them highly effective for desiccation purposes. This application is especially valuable in industries where moisture control is crucial, such as electronics and pharmaceuticals, where even a small amount of moisture can compromise the quality of the final product.
Exploring the Manufacturing Process
The manufacturing of ceramic balls is an intricate process that involves various steps to ensure their precision and performance.
Compression Molding
Starting from selecting the appropriate ceramic powder, the material undergoes compression molding to shape it into spherical forms. This step ensures uniformity in size and shape, which is critical for applications like bearings and grinding media.
Sintering
Following that, the balls are sintered at high temperatures to achieve their final hardness and strength. This process ensures that ceramic balls can meet the grinding efficiency and durability standards required for demanding applications.
Grinding and Polishing
Moreover, manufacturers also put ceramic balls through a series of precision grinding and polishing stages to achieve the required surface finish. The result is a product with an exceptionally smooth surface, which contributes to reduced friction in applications like high-speed bearings. This attention to detail is part of what makes ceramic balls a preferred choice in applications that require precision ceramic balls, such as medical and electronic devices.
Manufacturing Process of Ceramic Balls
Step | Description | Outcome |
Compression Molding | Shaping ceramic powder into spherical forms | Uniform size and shape |
Sintering | Heating to high temperatures to solidify and strengthen | Final hardness and strength |
Grinding and Polishing | Precision finishing to achieve smooth surface | Reduced friction, precision finish |
Frequently Asked Questions
What are ceramic balls?
Ceramic balls are spherical components made from industrial ceramic materials, known for their exceptional hardness, heat resistance, and chemical inertness. They are widely used in various industrial and engineering applications.
What types of ceramic balls are available?
There are several types of ceramic balls, including Silicon Nitride, Alumina, Zirconia, and Silica. Each type has unique properties and benefits for specific applications.
What are the main applications of ceramic balls?
Ceramic balls are used in a wide range of applications, including bearings, grinding media, filtration systems, valves, pumps, and desiccant solutions.
How are ceramic balls used in bearings?
Ceramic balls, particularly silicon nitride balls, are used in high-speed bearings due to their lightweight properties, high strength, and low friction, making them ideal for aerospace and automotive industries.
What makes ceramic balls suitable for grinding media?
Ceramic grinding media are highly wear-resistant and chemically inert, making them ideal for grinding and blending materials such as chemicals, ores, and powders without contamination.
What is the difference between ceramic balls and steel balls?
Ceramic balls are harder, lighter, and more heat-resistant than steel balls. They also offer better corrosion resistance and electrical insulation, while steel balls are generally more affordable and less brittle.
What are the advantages of using silicon nitride balls?
Silicon nitride balls are known for their high strength, wear resistance, and heat resistance, making them suitable for high-performance applications like aerospace and defense.
How do alumina balls differ from other ceramic balls?
Alumina balls are valued for their corrosion resistance and thermal stability, making them ideal for use in chemical industries where they encounter aggressive chemicals.
What are zirconia ceramic balls used for?
Zirconia ceramic balls have high fracture toughness and wear resistance, which makes them suitable for environments with mechanical shock, such as valves and pumps in the petrochemical industry.
Can ceramic balls be used in high-temperature environments?
Yes, high-temperature ceramic balls, such as those made from silicon nitride or alumina, are well-suited for environments where they are exposed to extreme heat, such as in furnaces or high-speed bearings.
What industries use ceramic balls?
Ceramic balls are used in industries like aerospace, automotive, oil & gas, chemical processing, food, and pharmaceuticals for various purposes, including bearings, filtration, and grinding.
Are ceramic balls corrosion-resistant?
Yes, ceramic balls are corrosion-resistant, especially alumina and zirconia balls, which are capable of withstanding harsh chemicals, acids, and salts, making them ideal for use in chemical processing.
How do ceramic balls contribute to grinding efficiency?
Ceramic balls provide excellent grinding efficiency due to their high hardness, wear resistance, and ability to grind without contaminating the material, which is crucial in sensitive industries like food and pharmaceuticals.
What are ceramic ball desiccants?
Ceramic ball desiccants, typically made from silica, are used to absorb moisture in various settings, such as electronics and pharmaceutical industries, to maintain product integrity.
What are precision ceramic balls?
Precision ceramic balls are manufactured with tight tolerances and high surface quality, making them suitable for high-precision applications such as bearings in medical devices and aerospace components.
How are ceramic balls manufactured?
Ceramic balls are manufactured through a process that includes compression molding, sintering at high temperatures, and precision grinding and polishing to achieve their final shape and properties.
What are the key properties of ceramic balls?
Ceramic balls possess several key properties, including high hardness, heat resistance, corrosion resistance, low density, and electrical insulation, making them versatile for many applications.
What are the advantages of using ceramic balls in valves and pumps?
Ceramic balls are used in valves and pumps due to their hardness, corrosion resistance, and ability to withstand harsh environments, which prolongs the lifespan of these components, especially in the petrochemical industry.
How do ceramic balls compare to steel in terms of weight?
Ceramic balls are generally lighter than steel balls, which reduces the overall weight of the machinery they are used in. This feature is particularly beneficial in aerospace and automotive applications.
What are the main challenges of using ceramic balls?
The main challenges of using ceramic balls include their brittleness, which makes them susceptible to cracking under impact, and their higher cost compared to steel balls, which can limit their use in cost-sensitive applications.
Conclusion: The Versatile World of Ceramic Balls
In conclusion, ceramic balls are a fascinating and highly versatile component of modern technology. Their unique properties, such as extreme hardness, resistance to corrosion, and lightweight nature, make them indispensable in a wide range of industries. Whether it’s their use in high-performance bearings, grinding media, filtration systems, or as ceramic valve components, ceramic balls provide solutions that outperform traditional materials in numerous ways.
The applications and benefits of ceramic balls make them a crucial part of modern industry. If you are interested in exploring ceramic balls for your own use or would like to know more about how these remarkable materials can enhance your business operations, please take a look at our detailed product offerings here. For more in-depth reading on the characteristics of ceramic balls under various conditions, I recommend this external research on cyclic fatigue life characteristics of ceramic balls under variable thermal shock loadings.
Feel free to check out the ceramic balls category that dives deeper into the use of ceramic materials and their broad-reaching impact on various sectors. Ceramic balls are more than just industrial components; they are the backbone of many modern innovations, and their future looks bright as industries evolve.
Disclaimer
The information in this article is intended for general informational purposes only. It should not be used as a substitute for professional advice in specific contexts or industries. Always consult a specialist to determine the most appropriate type of ceramic material for your needs.