The Regeneration Process of Activated Alumina: Techniques and Best Practices
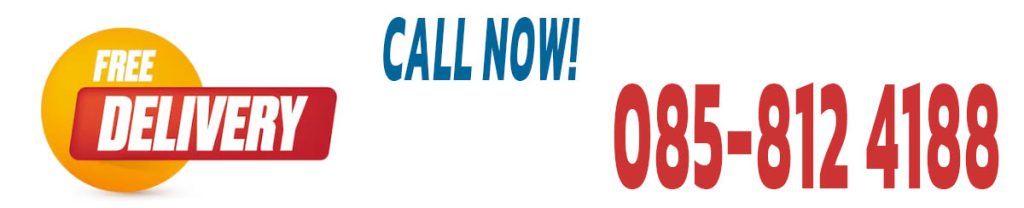
Table of Contents
I. Introduction
Activated alumina is a versatile adsorbent material used in a wide range of industrial applications, and proper regeneration is essential to maintaining its efficiency and longevity. This article will discuss the importance of activated alumina regeneration, the various techniques available, best practices to follow, and the challenges and limitations associated with the process.
II. The Importance of Activated Alumina Regeneration
A. Maintaining Adsorption Capacity
Regular regeneration of activated alumina is vital to maintain its adsorption capacity and ensure optimal performance in various applications. Over time, the alumina becomes saturated with adsorbed molecules, reducing its effectiveness. Regeneration allows for the removal of these molecules, restoring the activated alumina’s original capacity and enabling it to continue functioning efficiently.
B. Extending the Lifespan of Activated Alumina
With proper regeneration techniques, the lifespan of activated alumina can be significantly extended, reducing the need for frequent replacement and minimizing costs. A well-maintained activated alumina adsorbent can be used for several years, depending on the application and operating conditions. This not only saves on material costs but also reduces the environmental impact associated with the disposal of spent alumina.
III. Regeneration Techniques
There are several methods available for regenerating activated alumina, each with its own advantages and disadvantages. The choice of technique will depend on factors such as the specific application, operating conditions, and budget constraints.
A. Thermal Regeneration
Thermal regeneration is a widely used method for restoring the adsorption capacity of activated alumina by heating it to a high temperature. The heat causes the adsorbed molecules to desorb from the alumina surface, leaving it clean and ready for reuse. This process typically involves heating the activated alumina to temperatures between 200°C and 350°C in a controlled environment, such as a furnace or oven, for several hours.
Thermal regeneration is effective in removing a wide range of adsorbed contaminants and can be used for various applications, such as air and gas drying, catalyst support, and water treatment. However, it is an energy-intensive process, and care must be taken to avoid overheating, which can damage the activated alumina’s structure and reduce its performance.
B. Pressure Swing Adsorption (PSA)
Pressure swing adsorption (PSA) is another popular technique for regenerating activated alumina, involving rapid changes in pressure to facilitate desorption of adsorbed molecules. In this process, the activated alumina is exposed to alternating high and low-pressure cycles, causing the adsorbed molecules to be released from the alumina surface.
PSA is a highly effective regeneration technique for applications such as air separation and gas purification. It is more energy-efficient than thermal regeneration and can be easily automated, reducing labor and operational costs. However, it may not be suitable for all applications, as some adsorbed contaminants may not desorb effectively under the pressure changes.
C. Vacuum Regeneration
Vacuum regeneration is a method that employs reduced pressure to remove adsorbed molecules from activated alumina, making it suitable for applications with low-temperature requirements. In this process, a vacuum pump is used to create a low-pressure environment around the activated alumina, causing the adsorbed molecules to be released.
This technique is particularly useful for regenerating activated alumina used in applications sensitive to high temperatures, such as pharmaceuticals or electronics manufacturing. Vacuum regeneration is also energy-efficient, as it requires less heat input than thermal regeneration. However, it may not be as effective in removing certain types of adsorbed contaminants, and the process can be slower compared to other methods.
IV. Best Practices for Activated Alumina Regeneration
A. Monitoring and Scheduling
To ensure optimal performance and extend the lifespan of activated alumina, it is crucial to monitor its adsorption capacity and schedule regular regeneration based on the specific application and operating conditions. Factors such as temperature, humidity, and the presence of impurities can impact the rate at which the alumina becomes saturated. Regular monitoring allows for timely regeneration, preventing a decline in performance and potential damage to the activated alumina.
B. Pre-treatment
Before starting the regeneration process, it is essential to remove any residual liquid or large particles from the activated alumina. This pre-treatment step helps to prevent contamination or damage during regeneration and ensures a more effective process. Depending on the application, this may involve draining any remaining liquid or using a filter to remove larger particles.
C. Following Manufacturer Guidelines
When regenerating activated alumina, it is crucial to follow the manufacturer’s guidelines for the specific product being used. Different types of activated alumina may have unique properties or requirements, and adhering to the manufacturer’s recommendations will help to ensure optimal performance and longevity. This may include specific temperature or pressure settings, as well as recommended regeneration intervals.
D. Cooling and Storage
After the regeneration process is complete, it is essential to allow the activated alumina to cool down to room temperature before returning it to service. Rapid cooling can cause structural damage, reducing the material’s performance and lifespan. Once cooled, the regenerated activated alumina should be stored in a clean, dry environment to prevent contamination or degradation before reuse.
V. Challenges and Limitations of Activated Alumina Regeneration
While regeneration is a critical aspect of maintaining activated alumina’s performance and longevity, there are some challenges and limitations associated with the process.
A. Energy Consumption
Regeneration methods such as thermal regeneration and vacuum regeneration can be energy-intensive, leading to higher operating costs and environmental impacts. To minimize energy consumption and ensure energy efficiency, it is crucial to choose the most efficient regeneration method for the specific application and optimize the process to reduce energy waste.
B. Potential Damage to Activated Alumina
Improper regeneration techniques or conditions can cause damage to the activated alumina, reducing its performance and lifespan. Factors such as overheating during thermal regeneration or rapid cooling after the process can result in structural damage or a decrease in adsorption capacity. To prevent this, it is essential to follow best practices and manufacturer guidelines when regenerating activated alumina.
C. Incomplete Regeneration
In some cases, the regeneration process may not effectively remove all adsorbed contaminants from the activated alumina, leading to a decrease in performance. This can be due to the specific properties of the adsorbed molecules, the regeneration method used, or improper regeneration conditions. To ensure complete regeneration, it is crucial to choose the most suitable method for the application and optimize the process based on the specific adsorbed contaminants.
VI. Conclusion: Maximizing the Performance and Lifetime of Activated Alumina
Proper regeneration of activated alumina is essential to maintaining its adsorption capacity, performance, and lifespan in various industrial applications. By understanding the different regeneration techniques, following best practices, and addressing the challenges and limitations associated with the process, users can maximize the potential of activated alumina and minimize costs and environmental impacts.
VII. Frequently Asked Questions
Can activated alumina be regenerated?
Yes, activated alumina can be regenerated through various techniques, including thermal regeneration, vacuum regeneration, and pressure swing adsorption.
What is the manufacturing process of activated alumina?
Activated alumina is produced through the dehydration of aluminum hydroxide, typically through calcination at high temperatures.
What is the lifespan of activated alumina?
The lifespan of activated alumina can vary depending on the application, operating conditions, and maintenance practices. Regular regeneration can significantly extend its lifespan.
What is the purpose of activated alumina?
Activated alumina is used for various applications, including adsorption, desiccation, water treatment, and as a catalyst support in the petrochemical industry.
What are the disadvantages of activated alumina?
Some disadvantages of activated alumina include potential performance degradation due to impurities, energy-intensive regeneration processes, and sensitivity to temperature and humidity conditions.
At what temperature does alumina degrade?
Alumina can begin to degrade at temperatures above 1000°C (1832°F).
What is the annealing temperature of alumina?
The annealing temperature for alumina typically ranges between 1300°C to 1600°C (2372°F to 2912°F).
What is the difference between alumina and activated alumina?
Alumina is a general term for aluminum oxide, while activated alumina is a highly porous, adsorbent form of alumina created through the dehydration of aluminum hydroxide.
What temperature does alumina activate?
Alumina is typically activated at temperatures ranging between 300°C and 600°C (572°F and 1112°F).
Which process is used to purify alumina?
The Bayer process is commonly used to purify alumina from bauxite ore.
What is activated alumina filtration?
Is activated alumina activated by heating?
Yes, activated alumina is produced by heating aluminum hydroxide to remove water molecules, creating a highly porous structure.
What is the pH of activated alumina?
The pH of activated alumina varies depending on the specific product and its application, but it generally ranges between 4 and 8.
Does activated alumina absorb water?
Yes, activated alumina can absorb water due to its highly porous structure and is commonly used as a desiccant for drying gases and liquids.
What is the risk of alumina?
The primary risk of alumina is inhalation of fine particles, which can cause respiratory irritation. Proper handling and safety precautions should be followed to minimize exposure.
Why is alumina highly stable?
Alumina is highly stable due to its strong chemical bonds, high melting point, and resistance to thermal shock.
What is alumina refining?
Alumina refining is the process of extracting and purifying alumina from bauxite ore, typically using the Bayer process.
How do you recharge activated alumina?
Activated alumina can be recharged through various regeneration techniques, such as thermal regeneration, vacuum regeneration, or pressure swing adsorption.
How much water can activated alumina absorb?
Activated alumina can typically absorb up to 20% of its weight in water, but this can vary depending on the specific product, operating conditions, and humidity levels.
What does activated alumina remove from water?
Activated alumina removes various contaminants from water, including fluoride, arsenic, selenium, phosphates, and heavy metals.
What is activated alumina very much effective for the removal of?
Activated alumina is highly effective in removing fluoride, arsenic, and other contaminants from water. It is also effective in drying gases and liquids and as a catalyst support in various industrial processes.
Factors Affecting the Performance and Lifetime of Activated Alumina
Comparing Activated Alumina with Other Desiccants: Silica Gel, Molecular Sieve, and Activated Carbon
A Comprehensive Guide to Activated Alumina
https://www.sciencedirect.com/science/article/pii/S1350417720312682
ขอบคุณที่ใช้เวลาอ่านบทความของเราเกี่ยวกับการป้องกันความชื้น ทางเราหวังว่าท่านจะได้รับข้อมูลที่มีคุณค่าและเป็นประโยชน์ ทางเรายินดีให้บริการการปรึกษาฟรีเพื่อพูดคุยเกี่ยวกับความต้องการของท่านและให้คำแนะนำเกี่ยวกับวิธีการป้องกันความชื้นที่กำหนดเฉพาะสำหรับคุณ โปรดติดต่อเราที่ 0858124188 เพื่อนัดหมายการปรึกษาหรือเยี่ยมชมร้านค้าของเราเพื่อค้นหาผลิตภัณฑ์ที่ช่วยป้องกันสินค้าของคุณจากความเสียหายจากความชื้น ทางเราหวังว่าจะได้รับข่าวสารจากท่านเร็วๆนี้