Adsorption Solutions with Molecular Sieves: Targeting VOCs, Ammonia, and Sulfur Compounds
Topic | Details |
---|---|
VOCs Adsorption | Molecular sieves capture VOCs effectively, ideal for applications in chemical, paint, and pharmaceutical industries. |
Ammonia Adsorption | 3A sieves are well-suited for ammonia removal, making them useful in refrigeration and wastewater treatment. |
Sulfur Compound Adsorption | Sulfur compounds, including H₂S, can be removed efficiently in gas processing applications using 13X sieves. |
Operational Optimization | Adjusting temperature, pressure, and flow rate maximizes molecular sieve efficiency for specific gas adsorption tasks. |
Maintenance & Regeneration | Regular regeneration helps prolong molecular sieve effectiveness, ensuring consistent adsorption of VOCs, ammonia, and sulfur compounds. |
Table Of Contents
“For industries where purity and safety are critical, molecular sieves offer unparalleled adsorption solutions, keeping processes clean and compliant at every stage.”
Introduction
In industries where air quality, chemical purity, and regulatory compliance are essential, targeted gas purification solutions are critical. Molecular sieves provide a powerful and versatile option for selectively adsorbing various gases and impurities, including volatile organic compounds (VOCs), ammonia, and sulfur compounds. Each of these compounds presents unique challenges that molecular sieves can help address effectively, making them indispensable in settings like petrochemical processing, environmental protection, and food production.
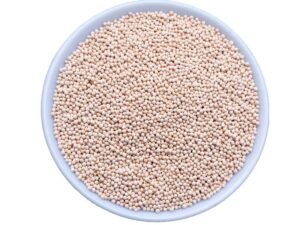
To get familiar with the different types of molecular sieves and how they function, refer to our Comprehensive Guide to Molecular Sieves.
Understanding the Role of Molecular Sieves in Targeted Gas Adsorption
Molecular sieves are synthetic zeolites with highly ordered structures and specific pore sizes that allow them to capture molecules of a defined size. This makes them uniquely effective for selective adsorption of gases, including VOCs, ammonia, and sulfur compounds, where other adsorbents like activated carbon or silica gel may fall short. Their adsorption properties are dictated by the size and polarity of the target molecules, with each sieve type—3A, 4A, 5A, and 13X—optimally suited for different industrial needs.
When used in industrial gas purification, molecular sieves enhance safety, product quality, and regulatory compliance, especially in highly regulated sectors such as pharmaceuticals, chemical production, and food processing. For detailed insights on storing these materials to maximize their lifespan, visit our post on Packaging and Storage of Molecular Sieves.
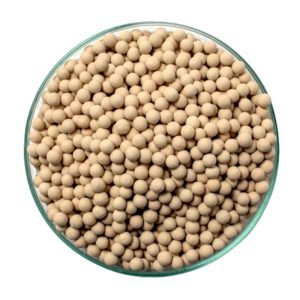
Adsorption Solutions with Molecular Sieves for Volatile Organic Compounds (VOCs)
Comparison of Molecular Sieve Types for VOC, Ammonia, and Sulfur Compound Adsorption
Molecular Sieve Type | Target Compound(s) | Ideal Industries | Key Feature |
---|---|---|---|
Molecular Sieves 3A | Ammonia | Refrigeration, wastewater treatment | Selective ammonia adsorption |
Molecular Sieves 4A | Small hydrocarbons | Gas purification, petrochemical processing | Balanced moisture and gas adsorption |
Molecular Sieves 5A | VOCs | Paint, chemical, pharmaceutical | Optimal for hydrocarbon adsorption |
Molecular Sieves 13X | Sulfur compounds, VOCs | Natural gas, petroleum refining | Larger pore size for diverse compounds |
The Challenge of VOCs in Industrial Settings
VOCs pose risks to air quality, environmental safety, and worker health. Prevalent in paints, solvents, and coatings, VOCs readily evaporate, requiring effective adsorption solutions to prevent contamination. Molecular sieves provide a targeted adsorption solution for VOCs, effectively capturing these compounds from gas streams and providing a safer industrial environment.
Mechanisms of VOC Adsorption with Molecular Sieves
With pore structures optimized for selective adsorption, molecular sieves—particularly 5A and 13X types—serve as efficient adsorption solutions for VOCs. For example, 5A sieves are ideal for capturing hydrocarbons, while the larger pores of 13X sieves trap larger VOC molecules, providing versatile solutions for diverse industrial needs.
Use Cases in Industry
Paint manufacturing, pharmaceuticals, and chemicals are just some of the sectors that benefit from these VOC-targeting adsorption solutions. Pharmaceutical applications rely on molecular sieves to capture VOCs and prevent contamination, while paint and coatings industries use them to protect air quality in confined production environments. For detailed guidance on selecting the right molecular sieve type, visit our Molecular Sieves Types and Applications.
Adsorption Solutions with Molecular Sieves for Ammonia
The Importance of Ammonia Adsorption in Industry
Industries like refrigeration, petrochemicals, and wastewater treatment frequently manage ammonia emissions. Left unchecked, ammonia poses risks of corrosion, strong odor, and environmental contamination. Adsorption solutions with molecular sieves—specifically 3A sieves—offer efficient ammonia removal, ensuring safe, odor-free environments and preventing equipment damage.
Selecting the Right Molecular Sieve for Ammonia Adsorption
3A molecular sieves are among the most effective adsorption solutions for ammonia, with a pore size that allows ammonia molecules to be selectively trapped while allowing other compounds to pass through. These properties make 3A sieves ideal for industries with specific ammonia control needs.
Case Studies in the Petrochemical and Wastewater Treatment Sectors
Petrochemical plants and wastewater facilities frequently rely on 3A molecular sieves for ammonia adsorption. In petrochemicals, 3A sieves help maintain equipment by preventing corrosive ammonia buildup. In wastewater treatment, they prevent nitrogen-based pollution, contributing to environmentally sustainable operations.
Adsorption Solutions with Molecular Sieves for Sulfur Compounds
Challenges of Sulfur Compound Adsorption in Industrial Applications
Sulfur compounds, particularly hydrogen sulfide (H₂S), are toxic, odorous, and corrosive, making their removal critical in industries such as natural gas processing and petroleum refining. Using molecular sieves as adsorption solutions for sulfur compounds is effective in removing these harmful gases from process streams.
How Molecular Sieves Capture Sulfur Compounds
13X molecular sieves are ideally suited for sulfur compound adsorption, with larger pore sizes that accommodate sulfur-based molecules. By capturing H₂S and similar sulfur compounds, 13X sieves improve gas purity, reduce equipment corrosion, and provide safe handling conditions.
Industrial Applications
In natural gas processing and petroleum refining, the presence of sulfur compounds can significantly impact product quality and safety. Adsorption solutions with molecular sieves ensure that H₂S is captured efficiently, meeting purity standards and reducing environmental impact.
Industrial Applications and Relevant Molecular Sieve Selection
Industry | Key Compound for Removal | Recommended Molecular Sieve |
---|---|---|
Pharmaceutical Industry | VOCs | Molecular Sieves 13X |
Petrochemical Industry | Ammonia, sulfur compounds | Molecular Sieves 3A, Molecular Sieves 13X |
Natural Gas Processing | Sulfur compounds | Molecular Sieves 13X |
Paint Manufacturing | VOCs | Molecular Sieves 5A |
Wastewater Treatment | Ammonia | Molecular Sieves 3A |
Key Considerations for Effective Adsorption Solutions with Molecular Sieves
Choosing the Right Molecular Sieve Type
The right molecular sieve type is crucial to effective adsorption. For instance, 5A molecular sieves provide hydrocarbon adsorption, 3A sieves target ammonia, and 13X sieves capture VOCs and sulfur compounds, making them ideal adsorption solutions for each application. This understanding enables industries to select the optimal solution for their specific needs.
Optimizing Operational Conditions
Adjusting conditions such as temperature, pressure, and flow rate is essential to maximize the efficiency of adsorption solutions with molecular sieves. Higher pressures and lower temperatures generally enhance adsorption, making processes more efficient and reducing operational costs.
Steps for Optimizing Adsorption with Molecular Sieves
- Select the Appropriate Sieve Type: Choose based on target compounds (e.g., 3A for ammonia, 13X for VOCs).
- Control Temperature: Lower temperatures generally enhance adsorption efficiency.
- Adjust Pressure: Increase pressure to improve adsorption, but ensure system compatibility.
- Monitor Flow Rate: Maintain a steady, optimized flow rate for thorough gas contact with the sieve surface.
Optimal Operational Conditions for Molecular Sieve Efficiency
Condition | Effect on Adsorption | Recommended Setting |
---|---|---|
Temperature | Lower temperature enhances adsorption | 20-25°C |
Pressure | Higher pressure improves capacity | Industry-specific (adjust as needed) |
Flow Rate | Slower rate allows for thorough adsorption | Adjusted based on system size |
Regeneration Frequency | Restores adsorption capacity | Every 1-2 weeks (or as needed) |
Maintenance and Regeneration
Regular maintenance and regeneration are necessary for sustaining molecular sieve effectiveness. During regeneration, absorbed compounds are removed, restoring the sieve’s capacity for adsorption. For more information on this critical process, visit our article on Regeneration and Reuse of Molecular Sieves.
Indicators That Molecular Sieves Require Regeneration
- Decreased Adsorption Efficiency: Lowered adsorption capacity may indicate saturation.
- Physical Changes in Sieves: Attrition or a dusty appearance suggests the need for regeneration.
- Increased System Pressure: Higher pressure may occur if the sieve bed is clogged with adsorbed compounds.
- Change in Gas Purity: If target compounds are detected post-sieve, regeneration may be needed.
Common Challenges and Solutions in Molecular Sieve Adsorption
Challenge | Solution |
---|---|
Reduced adsorption capacity | Regular regeneration using controlled heating |
Contamination from residual gases | Ensure proper initial drying and storage conditions |
Physical degradation (attrition) | Use sieves with high crush strength for durability |
Uneven gas distribution | Optimize flow rate and uniform distribution system |
Adsorption and Beyond: Key Molecular Sieve Processes
While adsorption is a primary application of molecular sieves, these versatile materials support a wide array of industrial processes. From gas drying and separation to catalytic support, molecular sieves provide solutions that enhance purity, efficiency, and product quality across various applications. Understanding these key processes offers a fuller picture of how molecular sieves drive industry innovation.
To explore these core processes in detail and see how molecular sieves are applied across industries, visit our page on Key Molecular Sieve Processes.
When considering molecular sieves for adsorption solutions, understanding the specific contaminant, adsorption environment, and required purity level is essential. Molecular sieves’ versatile adsorption capabilities extend beyond gas and air treatment, playing a crucial role in water purification where they target contaminants such as heavy metals, VOCs, and dissolved gases. For a comprehensive look at how molecular sieves are utilized in water treatment applications, see Molecular Sieves in Water Treatment: Ensuring Safe, Clean Water.
Frequently Asked Questions
What are adsorption solutions with molecular sieves?
Adsorption solutions with molecular sieves involve using sieves with precise pore sizes to capture specific gases or compounds, such as VOCs, ammonia, and sulfur compounds, from industrial gas streams. These solutions help achieve high purity and control emissions effectively.
How do molecular sieves work for volatile organic compounds (VOC) adsorption?
Molecular sieves adsorb VOCs by trapping the molecules within their uniform pores. Sieves like 5A and 13X are effective for VOC adsorption due to their specific pore sizes, which allow them to capture VOC molecules selectively.
Why are molecular sieves preferred for ammonia removal?
Molecular sieves, especially 3A, are ideal for ammonia removal due to their small, selective pore sizes, which adsorb ammonia molecules effectively while allowing other gases to pass through. This makes them valuable for applications like refrigeration and wastewater treatment.
What are sulfur compound adsorption solutions?
Sulfur compound adsorption solutions use molecular sieves, like 13X, to capture sulfur-based gases such as hydrogen sulfide (H₂S) in gas purification processes. These sieves prevent corrosion and ensure safer handling of sulfur-laden gas streams.
Which molecular sieve is best for volatile organic compound adsorption?
5A and 13X molecular sieves are commonly used for VOC adsorption due to their pore sizes and adsorption capacity, which are well-suited to trap hydrocarbons and larger organic compounds found in industrial emissions.
Can molecular sieves be used for gas separation?
Yes, molecular sieves are often used in gas separation. They selectively adsorb specific gases based on molecular size and polarity, making them effective for separating components like nitrogen, oxygen, and moisture from gas streams.
What are some industrial applications of molecular sieves?
Molecular sieves are widely used in industries such as petrochemicals, pharmaceuticals, natural gas processing, and environmental protection. They help purify gases, control emissions, and maintain product quality in these settings.
How is ammonia removed with molecular sieves?
Ammonia removal with molecular sieves, especially 3A, involves trapping ammonia molecules in the sieve’s pores. This process, called the ammonia adsorption process, prevents ammonia from causing corrosion or contamination in various industrial applications.
What are the benefits of using VOC adsorption technology in industry?
VOC adsorption technology with molecular sieves reduces air pollution, enhances worker safety, and helps industries comply with environmental regulations. It also maintains product purity by capturing unwanted volatile organic compounds.
How do molecular sieves differ from other adsorbents in sulfur removal technology?
Molecular sieves have uniform pore sizes that allow selective adsorption of sulfur compounds, providing more targeted and effective removal than other adsorbents like activated carbon, which may not capture sulfur compounds as efficiently.
Can molecular sieves be regenerated after VOC, ammonia, or sulfur compound adsorption?
Yes, molecular sieves can be regenerated by removing adsorbed compounds through heating or applying a vacuum. This process restores their adsorption capacity, making them reusable for multiple cycles.
What factors influence the efficiency of molecular sieves in gas purification?
Factors like temperature, pressure, flow rate, and the type of molecular sieve all impact efficiency. Optimizing these conditions ensures maximum adsorption capacity and longer sieve lifespan in gas purification.
How does molecular sieve adsorption improve industrial gas purification?
By capturing specific gases like VOCs, ammonia, and sulfur compounds, molecular sieves enhance gas purity, protect equipment from corrosion, and reduce emissions, ensuring higher product quality and compliance with safety standards.
What industries benefit most from molecular sieve applications?
Industries like petrochemical, natural gas processing, pharmaceuticals, and environmental protection benefit from molecular sieve applications due to their need for precise gas purification and control of contaminants.
Why are 13X molecular sieves often used for sulfur compound adsorption?
13X molecular sieves are suited for sulfur compound adsorption due to their larger pore size, which can effectively capture larger sulfur-based molecules like hydrogen sulfide, common in natural gas and petroleum refining.
How does the pore size of a molecular sieve impact adsorption solutions?
The pore size determines which molecules can be adsorbed by the sieve. For example, 3A sieves target small molecules like ammonia, while 13X sieves capture larger compounds like VOCs and sulfur compounds, providing tailored adsorption solutions.
What is the typical lifespan of a molecular sieve used for gas separation?
The lifespan varies depending on factors such as usage frequency, regeneration practices, and gas types. Proper maintenance and regular regeneration can extend the lifespan, making them effective for several years in industrial settings.
Are there specific storage conditions for molecular sieves?
Molecular sieves should be stored in a dry, sealed container to prevent moisture adsorption before use. Proper storage maintains their adsorption efficiency and longevity. For more on this, see our guide on Packaging and Storage of Molecular Sieves.
What are common issues encountered with molecular sieve adsorption solutions?
Common issues include reduced adsorption capacity due to saturation, contamination from residual gases, and physical degradation. Regular regeneration and proper maintenance help resolve these issues.
How do adsorption solutions with molecular sieves contribute to environmental sustainability?
Molecular sieves reduce harmful emissions by capturing VOCs, ammonia, and sulfur compounds from industrial gases. This process helps industries minimize their environmental impact, comply with regulations, and maintain a sustainable operation.
“Molecular sieves are essential for industrial gas purification, capturing harmful VOCs, ammonia, and sulfur compounds with precision that other adsorbents can’t match.”
Conclusion
Industries requiring gas purification rely on adsorption solutions with molecular sieves to control VOCs, ammonia, and sulfur compounds. By selecting the correct molecular sieve type, industries can enhance purity, protect equipment, and meet regulatory standards.
Explore our full Molecular Sieve Product Page to find the right molecular sieve product for your unique requirements.
For a more comprehensive understanding of molecular sieves, refer to our Comprehensive Guide to Molecular Sieves, or consult ScienceDirect’s Molecular Sieves for more detailed insights on adsorption applications. Also check out our previous pages: Optimizing Gas Purity: Molecular Sieve Solutions for Separation, Drying, and Purification and Hydrocarbon Separation and Refining: How Molecular Sieves Enhance Fuel Quality.