Key Molecular Sieve Processes: Applications and Industry Impact
Process | Description | Primary Molecular Sieve | Key Benefits |
---|---|---|---|
Adsorption | Captures VOCs, ammonia, sulfur compounds, and moisture from gases and liquids | Molecular Sieves 13X, Molecular Sieves 4A, Molecular Sieves 5A | Enhances product quality, equipment longevity |
Gas Separation | Separates gases like nitrogen and oxygen, enabling high-purity gas production | Molecular Sieves 5A, MSOX | Provides cost-effective, reusable solutions |
Industrial Gas Drying | Removes water vapor to prevent corrosion and freezing in pipelines | Molecular Sieves 3A, Molecular Sieves 4A | Ensures operational reliability across applications |
PSA Oxygen Generation | Produces concentrated oxygen by adsorbing nitrogen | Molecular Sieves 5A, MSOX | Essential for healthcare and manufacturing |
Catalytic Support | Stabilizes catalysts in chemical reactions, enhancing yield and efficiency | Molecular Sieves 13X, SSZ-13, ZSM-5 | Supports petrochemical refining and specialty chemicals |
Product Preservation | Controls moisture to prevent spoilage in packaging for food and electronics | Molecular Sieves 3A, Molecular Sieves 4A | Extends shelf life, maintains product quality |
Hydrocarbon Separation | Separates straight-chain from branched hydrocarbons, improving fuel quality | Molecular Sieves 5A | Essential for high-octane fuel production |
Environmental Control | Adsorbs pollutants from emissions, supporting VOC control and cleaner operations | Molecular Sieves 13X | Aids regulatory compliance and air quality improvement |
Table Of Contents
“From preserving food to producing medical-grade oxygen, molecular sieves power essential processes that impact every industry.”
Introduction
Molecular sieve processes are indispensable across various industrial applications due to their ability to selectively adsorb molecules based on size and polarity. This unique capability enables processes essential for everything from gas drying to advanced chemical reactions, providing a foundation for efficient production, quality control, and regulatory compliance. In this article, we’ll explore the primary molecular sieve processes and examine how they contribute to operational efficiency and environmental sustainability in industries like healthcare, petrochemicals, and food preservation.
For an overview of molecular sieve types and their applications, see A Comprehensive Guide to Molecular Sieve.
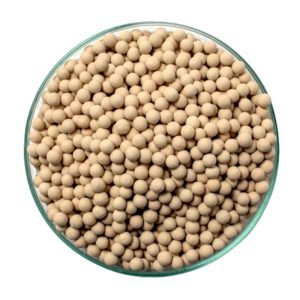
Adsorption Processes with Molecular Sieves
Key Point | Description |
---|---|
Objective | Capture contaminants from gas or liquid mixtures to ensure product quality and process efficiency |
Primary Contaminants | VOCs, ammonia, sulfur compounds, moisture |
Benefits | Improves safety, extends equipment life, enhances product purity |
Industry Application | Petrochemical refineries, pharmaceuticals, chemical processing |
Adsorption is a cornerstone molecular sieve process in which sieves capture specific molecules from gas or liquid mixtures, acting as highly selective “molecular sponges.” By removing contaminants such as VOCs, ammonia, and sulfur compounds, molecular sieves contribute significantly to product quality, equipment longevity, and safety. This selectivity makes them ideal for industries where even trace contaminants can lead to process inefficiencies or compromise product integrity.
Key Contaminants Removed Through Adsorption
- Volatile Organic Compounds (VOCs)
- Ammonia
- Sulfur compounds (e.g., H₂S, SO₂)
- Moisture
In petrochemical refineries, for instance, adsorption processes using molecular sieves can reduce sulfur compounds in fuel, helping to meet stringent environmental standards. The pharmaceutical industry also benefits from molecular sieve adsorption, where they purify air and gases to prevent contamination during drug production. This ensures that end products meet health and safety regulations, highlighting how molecular sieve processes are essential to operational success in multiple fields.
To dive deeper into adsorption solutions and see how molecular sieves capture specific contaminants, explore Adsorption Solutions with Molecular Sieves: Targeting VOCs, Ammonia, and Sulfur Compounds.
Gas Separation with Molecular Sieves
Key Point | Description |
---|---|
Objective | Separate gases by molecular size and polarity to produce high-purity gas streams |
Primary Molecular Sieves | Molecular Sieves 5A, MSOX |
Benefits | High-purity output, cost-effective, reusable, and compact systems for onsite production |
Industry Application | Healthcare (oxygen concentrators), food preservation (nitrogen), hydrogen for fuel cells |
Molecular sieves are crucial in gas separation processes, where their ability to distinguish gases by molecular size and polarity enables high-purity gas production. Industries like healthcare and food processing rely on this molecular sieve process for creating oxygen and nitrogen streams that meet strict purity standards. Molecular sieves such as Molecular Sieves 5A and MSOX are commonly used to capture nitrogen from air, leaving behind an oxygen-rich stream essential for oxygen concentrators in medical settings.
Advantages of Gas Separation with Molecular Sieves
- High-purity gas output (e.g., oxygen, nitrogen)
- Cost-effective compared to cryogenic methods
- Reusable through regeneration
- Compact systems suitable for onsite gas production
In manufacturing, gas separation plays a critical role in creating high-purity hydrogen for fuel cells and nitrogen for food preservation. By selectively adsorbing gases like nitrogen or CO₂, molecular sieve processes facilitate industrial operations requiring pure gas inputs. This precision reduces the need for additional purification steps, making molecular sieves a cost-effective, efficient choice for gas separation across industries.
Comparison of Molecular Sieve Types for Gas Separation
Molecular Sieve Type | Target Gas for Separation | Primary Application | Learn More |
---|---|---|---|
5A | Nitrogen | Oxygen concentrators, medical use | Molecular Sieves 5A |
4A | CO₂ | Natural gas purification | Molecular Sieves 4A |
3A | Moisture | Dehydration for gases like natural gas | Molecular Sieves 3A |
13X | VOCs | Environmental emissions control | The Versatility of 13X Molecular Sieves |
MSOX | Oxygen | Medical oxygen generation, PSA systems | The Power of MSOX Molecular Sieves |
For an in-depth look at this application, visit Gas Separation with Molecular Sieve.
Hydrogen Purification and Clean Energy Applications
Hydrogen purification has become increasingly critical as industries shift toward clean energy sources. Molecular sieves play an essential role in achieving high-purity hydrogen, especially in applications where impurities like CO and CO₂ must be carefully removed to support fuel cell efficiency and sustainability initiatives. For a deeper look at how molecular sieves enable efficient hydrogen purification and enhance green energy efforts, visit our page on Molecular Sieves for Hydrogen Purification.
Biogas Upgrading
Key Point | Description |
---|---|
Objective | Purify biogas by removing CO₂ and H₂S |
Primary Molecular Sieves | Molecular Sieves 13X, SSZ-13 |
Benefits | High-quality methane production, renewable energy support |
Industry Application | Biogas production, renewable energy sectors |
Biogas upgrading requires precise CO₂ and H₂S removal to produce high-quality methane for energy applications. Molecular sieves like 13X and SSZ-13 are highly effective in this process, capturing contaminants while allowing methane to pass through. This selective adsorption improves the methane content of biogas, making it suitable for use as a renewable energy source in industrial applications. SSZ-13’s CHA framework offers enhanced CO₂ adsorption, optimizing purity in biogas outputs.
Using molecular sieves in biogas purification helps industries reduce reliance on fossil fuels by refining biogas into a cleaner, more efficient fuel source. The process also contributes to reduced greenhouse gas emissions, as SSZ-13 and 13X capture CO₂ and sulfur compounds effectively. With an enhanced capacity for selective adsorption, molecular sieves support sustainable energy production in sectors focused on renewable fuels.
Industrial Gas Drying
Key Point | Description |
---|---|
Objective | Remove water vapor from gas streams to prevent equipment damage and product contamination |
Primary Molecular Sieves | Molecular Sieves 3A, Molecular Sieves 4A |
Benefits | Prevents corrosion, freezing, and unwanted chemical reactions, ensuring reliable operations |
Industry Application | Natural gas pipelines, compressed air systems, pharmaceuticals, chemical manufacturing |
Industrial gas drying, also known as dehydration, is an essential molecular sieve process where moisture can compromise product quality or cause equipment damage. Molecular sieves excel in this process by removing water vapor from gas streams, preventing issues like corrosion, freezing, and unwanted chemical reactions. In natural gas pipelines, for example, 3A molecular sieves are used to remove moisture, preventing clogs that could occur from ice formation during cold conditions.
Beyond natural gas, molecular sieves are also valuable in compressed air systems, where they keep industrial tools and equipment safe from moisture-related damage. By consistently drying gases to a high standard, molecular sieves ensure smooth operation across multiple applications. Whether used in pharmaceuticals, chemicals, or energy production, gas drying with molecular sieves is crucial for quality control and operational reliability.
Learn more about how molecular sieves enhance gas drying in The Benefits of Using Molecular Sieves in Gas Drying Applications.
Molecular Sieves for Air Drying and Purification
Molecular Sieves for Air Drying utilize advanced adsorption techniques to capture moisture and impurities efficiently. Their selective adsorption mechanism—choosing only specific molecules to bind—makes them a preferred choice in applications requiring precise moisture control. Industries that rely on compressed air, such as food processing and pharmaceutical production, benefit significantly from this technology, as molecular sieves ensure consistent, clean air output.
As industries evolve, the demand for high-purity air and moisture control grows, pushing molecular sieve technology toward greater innovation. The future of molecular sieves in air drying and purification lies in enhanced adsorption capacity, improved energy efficiency, and sustainable practices that support the increasing emphasis on clean, eco-friendly industrial solutions. For a closer look, explore the complete Molecular Sieves for Air Drying and Purification post.
Moisture Control in Electronics Manufacturing
Key Point | Description |
---|---|
Objective | Maintain ultra-dry conditions for sensitive electronics |
Primary Molecular Sieves | Molecular Sieves 3A, Molecular Sieves 4A |
Benefits | Prevents oxidation, ensures product quality |
Industry Application | Electronics and semiconductor manufacturing |
Electronics manufacturing requires an ultra-dry environment, as even trace moisture can impact the performance and longevity of sensitive components. Molecular sieves, particularly 3A and 4A, are essential in creating and maintaining these controlled atmospheres. By adsorbing residual moisture in production areas, molecular sieves prevent oxidation and contamination in semiconductor and electronic assembly processes, safeguarding product quality.
In addition to creating moisture-free environments, molecular sieves also prevent electrostatic discharge and other moisture-related issues that could compromise electronic performance. As the industry continues to advance toward more intricate and sensitive devices, molecular sieves play a critical role in ensuring stable, dry manufacturing conditions for high-tech equipment.
PSA Oxygen Generation
Key Point | Description |
---|---|
Objective | Generate high-purity oxygen by selectively adsorbing nitrogen |
Primary Molecular Sieve | Molecular Sieves 5A, MSOX |
Industries Using PSA Oxygen | Healthcare, metalworking, pharmaceuticals, environmental treatment |
Benefits | Continuous, cost-effective oxygen production; eliminates bottled gas |
Process Advantage | Reliable on-site oxygen generation via pressure cycling |
The Pressure Swing Adsorption (PSA) process utilizes molecular sieves, specifically Molecular Sieves 5A and MSOX-500 / MSOX-501, to produce high-purity oxygen by selectively adsorbing nitrogen and leaving concentrated oxygen. These sieves are ideal due to their targeted selectivity and adsorption efficiency, making them essential for medical, industrial, and emergency oxygen needs. Alternating pressure cycles enable continuous oxygen production, a reliable and cost-effective solution for on-site applications.
Industries Relying on PSA Oxygen Generation
- Healthcare (e.g., hospitals)
- Metalworking and welding
- Pharmaceuticals and environmental treatment
In addition to healthcare, PSA oxygen generation is valuable in industries where combustion or oxidation is required, such as in metallurgy and chemical manufacturing. The PSA method’s efficiency, combined with the precise selectivity of molecular sieves, makes it a reliable choice for on-site oxygen production. This adaptability helps companies optimize oxygen availability without the costs associated with bottled gas, making PSA a cost-effective solution for diverse industries.
For an explanation of the PSA process, see The Science of PSA Oxygen Concentration.
Molecular Sieves for Carbon Capture and Environmental Applications
Molecular sieves are powerful tools in carbon capture and environmental sustainability, serving to reduce CO₂ emissions and purify gases across diverse industries. With their unique porous structures, these sieves selectively adsorb specific molecules, such as CO₂, moisture, and volatile organic compounds (VOCs), enabling efficient gas separation and drying. Key types, like 13X and 5A molecular sieves, are particularly effective in CO₂ capture and emission control, making them invaluable in applications ranging from industrial gas processing to automotive exhaust purification.
13X molecular sieves, with their high CO₂ adsorption capacity and larger pore sizes, are often the choice for CO₂ capture and greenhouse gas filtration. Meanwhile, 5A molecular sieves excel in hydrogen purification, biogas upgrading, and moisture removal, due to their slightly smaller pore size, which allows them to target a different range of molecules effectively. These sieves are also used extensively in pressure swing adsorption (PSA) systems, where they capture CO₂ and other gases from industrial emissions, supporting efforts to lower carbon footprints and meet environmental regulations.
In addition to reducing greenhouse gases, molecular sieves play a vital role in eco-friendly filtration across energy, automotive, and petrochemical industries. Their applications extend to purifying biogas, enhancing the purity of industrial gases, and ensuring the longevity of equipment by removing moisture. The renewable energy sector also relies on these sieves to upgrade biogas quality, making it suitable for fuel-grade use. Molecular sieves contribute to both environmental sustainability and operational efficiency by reducing emissions, supporting cleaner energy production, and enabling compliance with stringent environmental standards.
With their reusability and effectiveness in gas separation and drying, molecular sieves are a crucial element in achieving carbon reduction goals. Their adoption across industries illustrates their versatility and importance in today’s environmental landscape, where companies strive to balance productivity with sustainable practices.
For additional details, visit the full article on Molecular Sieves for Carbon Capture and Environmental Applications.
Catalytic Support in Chemical Reactions
Key Point | Description |
---|---|
Objective | Stabilize catalysts to improve yield and reaction efficiency |
Primary Molecular Sieve | Molecular Sieves 13X |
Benefits | Enhances reaction stability, reduces energy costs, and increases product quality |
Industry Application | Petrochemical refining, specialty chemical production, pharmaceuticals |
Molecular sieves serve as catalyst supports in chemical reactions, providing a stable, porous surface for catalytic agents. In petrochemical refining, for example, molecular sieves like 13X help facilitate reactions by stabilizing catalysts, which can improve yield and efficiency in complex chemical transformations. This role is crucial in the production of cleaner fuels and specialty chemicals, where stable reaction conditions directly impact product quality.
Beyond the petrochemical industry, catalyst support applications are also found in the production of fine chemicals and pharmaceuticals. Molecular sieves help maintain optimal conditions, allowing catalysts to work more effectively and enabling reactions to occur at lower temperatures. This process can reduce energy costs and improve overall efficiency, making molecular sieves an invaluable asset in chemical manufacturing.
While 13X is a prominent choice for catalytic support, other molecular sieves can also be effective depending on the reaction type and application:
- 13X: Ideal for general catalytic support in petrochemical and chemical refining, especially for stabilizing larger molecules.
- SSZ-13: Useful in catalytic applications requiring selective catalytic reduction (SCR) of NOx, commonly used in environmental and emissions control.
- ZSM-5: Often employed in hydrocarbon transformations and cracking processes due to its high stability and medium pore size.
Each type provides tailored support across industries like petrochemical refining, emissions control, and specialty chemical production.
Discover how molecular sieves work as catalyst supports in Molecular Sieve 13X Catalyst Support.
Hydrocarbon Isomerization
Key Point | Description |
---|---|
Objective | Convert straight-chain to branched hydrocarbons for higher octane fuel |
Primary Molecular Sieves | ZSM-5, SSZ-13 |
Benefits | Enhanced fuel quality, reduced emissions |
Industry Application | Petrochemical and refining sectors |
Hydrocarbon isomerization is a crucial process in refining, where straight-chain hydrocarbons are converted into branched isomers to enhance fuel quality, particularly for high-octane gasoline. Molecular sieves like ZSM-5 and SSZ-13 serve as catalytic supports in this process. Their selective pore structure allows for specific reactions that increase isomer yield, boosting fuel efficiency and reducing environmental impact. The structure of ZSM-5 and SSZ-13 enhances selectivity, making them ideal for optimizing hydrocarbon reactions.
In petrochemical applications, molecular sieves enable efficient conversion of hydrocarbons, supporting advanced refining techniques that meet modern fuel standards. The catalytic properties of these molecular sieves ensure effective conversion while minimizing unwanted by-products. Their stability under high temperatures also makes them well-suited for continuous isomerization processes, supporting a stable output for fuel production with improved octane ratings.
Hydrocarbon Separation and Purification
Key Point | Description |
---|---|
Objective | Isolate straight-chain hydrocarbons from branched ones to improve fuel quality |
Primary Molecular Sieve | Molecular Sieves 5A |
Benefits | Enables high-octane fuel production, cleaner combustion, and efficient fuel formulations |
Industry Application | Petrochemical refining and fuel production, ensuring quality control and consistency |
Hydrocarbon separation is a critical molecular sieve process in petrochemical and refining industries, where molecular sieves are used to isolate straight-chain hydrocarbons from branched-chain hydrocarbons. This separation improves fuel quality, enabling more efficient combustion and higher performance. In the refining process, Molecular Sieves 5A are particularly effective at separating normal paraffins from isoparaffins, a crucial step in producing high-octane fuels.
The effectiveness of molecular sieves in hydrocarbon separation also allows for more precise fuel formulations. By ensuring that each component meets strict purity requirements, molecular sieves contribute to the production of cleaner, more efficient fuels. This capability makes them essential in petrochemical production, where consistency and quality control are paramount.
For more information read Hydrocarbon Separation and Refining: How Molecular Sieves Enhance Fuel Quality
Product Preservation and Packaging
Key Point | Description |
---|---|
Objective | Maintain product stability by controlling moisture in packaging |
Primary Molecular Sieves | Molecular Sieves 3A, Molecular Sieves 4A |
Benefits | Extends shelf life, preserves quality, prevents spoilage and contamination |
Industry Application | Pharmaceuticals, electronics, food packaging |
Molecular sieves also play an essential role in product preservation processes by controlling moisture levels in packaging. In industries where product stability is crucial, such as pharmaceuticals and electronics, molecular sieves are used to keep goods free from moisture, thereby extending shelf life and preserving quality. By adsorbing residual moisture, molecular sieves prevent degradation, contamination, and spoilage.
In food packaging, molecular sieves help maintain freshness by reducing moisture that could otherwise lead to mold or spoilage. This use of molecular sieves in packaging not only enhances product quality but also reduces waste and loss. As consumer demand for high-quality, preservative-free products grows, molecular sieves offer a natural solution for product preservation across multiple sectors.
For more information on product preservation, visit Molecular Sieve and Product Preservation.
Ethanol Purity and Dehydration in Molecular Sieve Processes
Key Take-Away | Details |
---|---|
Importance of Purity | High-purity ethanol is essential for efficient fuel combustion and reduced emissions. |
Role of Molecular Sieves | 3A sieves enable selective water removal, achieving anhydrous ethanol ideal for fuel use. |
Renewable Energy Benefits | Pure ethanol supports biofuel industry goals for sustainability and efficiency. |
Selective Adsorption | Ensures water is removed without impacting ethanol, optimizing production quality and yield. |
In ethanol production, achieving high-purity, fuel-grade ethanol is critical, especially for applications in renewable energy and biofuels. Dehydration is a crucial step in ensuring ethanol’s performance, preventing issues like reduced combustion efficiency and system corrosion. Molecular sieves, particularly 3A sieves, enable efficient water removal by selectively adsorbing water molecules while allowing ethanol to pass through, ensuring the purity necessary for fuel applications. This selective adsorption process improves ethanol’s energy efficiency and aligns with industry demands for sustainable biofuel production. For a comprehensive look, see Molecular Sieves for Ethanol Dehydration: Ensuring Purity and Efficiency.
Environmental Impact and VOC Control
Key Point | Description |
---|---|
Objective | Capture pollutants like VOCs and sulfur compounds to improve air quality |
Primary Molecular Sieves | Molecular Sieves 13X |
Benefits | Reduces air pollution, aids regulatory compliance, contributes to a healthier environment |
Industry Application | High-emission industries, environmental sustainability initiatives |
Molecular sieves play a vital role in environmental protection processes by capturing pollutants like VOCs and sulfur compounds. This is particularly valuable in industries with high emissions, where sieves are used to adsorb harmful compounds from exhaust streams, reducing air pollution and improving air quality. By capturing VOCs and other volatile compounds, molecular sieves help companies adhere to environmental regulations and contribute to healthier working environments.
This molecular sieve process is especially relevant for industries committed to sustainability and emissions reduction. For example, 13X molecular sieves can capture VOCs from exhaust gases, enabling companies to comply with stricter environmental standards. With growing awareness of the impact of industrial pollution, molecular sieves are an effective solution for VOC control and emissions management.
To read about molecular sieves’ role in environmental protection, see The Environmental Impact of Molecular Sieves.
Regeneration and Reuse of Molecular Sieves
Regeneration Methods and Best Uses for Molecular Sieves
Regeneration Method | Best Use | Benefits |
---|---|---|
Heating | Gas drying, PSA systems | Restores adsorption capacity fully |
Vacuum Application | Oxygen concentrators, air separation units | Fast regeneration, low energy cost |
Steam Purging | Petrochemical, sulfur compound adsorption | Effective for high-load applications |
Pressure Swing | Continuous gas drying, oxygen generation | High efficiency in PSA processes |
A major advantage of molecular sieves is their ability to be regenerated for repeated use. After becoming saturated with adsorbed molecules, molecular sieves can be restored through heating or vacuum processes, which release the captured molecules and reset the sieves’ adsorption capacity. This reusability not only makes molecular sieves cost-effective but also reduces environmental waste by minimizing the need for replacement materials.
Benefits of Molecular Sieve Regeneration:
- Cost-effective due to reusability
- Reduced material waste
- Consistent performance with regular regeneration
- Environmental sustainability through reuse
Regeneration is especially beneficial in industries where molecular sieves are used continuously, such as in PSA systems for oxygen generation or in gas drying. By following proper regeneration techniques, companies can maintain the performance and lifespan of their molecular sieves, maximizing both investment value and sustainability. Regular regeneration practices are a key part of molecular sieve maintenance, making them a smart choice for long-term industrial use.
Learn about best practices for molecular sieve regeneration in Regeneration and Reuse of Molecular Sieves.
Frequently Asked Questions
What are molecular sieve processes?
Molecular sieve processes involve the use of molecular sieves to selectively adsorb, separate, dry, and purify gases and liquids. These processes are essential in industries such as healthcare, petrochemicals, and food packaging.
How do molecular sieves work in adsorption processes?
In adsorption processes, molecular sieves capture and hold specific molecules, such as VOCs or moisture, based on their size and polarity, effectively purifying the gas or liquid stream.
What is the difference between gas separation and gas drying with molecular sieves?
Gas separation isolates specific gases (e.g., oxygen from nitrogen), while gas drying removes water vapor from gases to prevent corrosion or freezing in pipelines.
What types of gases can be separated using molecular sieves?
Common gases separated using molecular sieves include oxygen and nitrogen, carbon dioxide from air, and hydrogen from gas mixtures, crucial for industries requiring high-purity gas streams.
How do molecular sieves contribute to product preservation?
Molecular sieves control moisture in packaging by adsorbing residual water vapor, which helps maintain product quality, extend shelf life, and prevent spoilage.
Why are molecular sieves used in Pressure Swing Adsorption (PSA) systems?
In PSA systems, molecular sieves selectively adsorb nitrogen at high pressure, leaving concentrated oxygen, making PSA ideal for on-site oxygen production in medical and industrial applications.
What role do molecular sieves play in petrochemical refining?
Molecular sieves aid in hydrocarbon separation and purification by isolating straight-chain from branched-chain hydrocarbons, improving fuel quality and efficiency in petrochemical processes.
How does molecular sieve regeneration work?
Molecular sieves are regenerated by heating or applying a vacuum to release adsorbed molecules, restoring their adsorption capacity and extending their lifespan.
Can molecular sieves be used to remove sulfur compounds?
Yes, molecular sieves can adsorb sulfur compounds such as hydrogen sulfide (H₂S), which is essential for refining and natural gas processing to meet environmental standards.
What are the benefits of using molecular sieves for VOC removal?
Molecular sieves effectively capture VOCs, reducing harmful emissions, improving air quality, and helping industries comply with environmental regulations.
How long do molecular sieves typically last?
Molecular sieves can last several years with proper use and regular regeneration, but lifespan depends on factors like contaminant levels, operational conditions, and maintenance.
Which industries rely most on molecular sieve processes?
Industries such as healthcare, petrochemicals, food and beverage, pharmaceuticals, and environmental services heavily rely on molecular sieve processes for purification, separation, and drying.
What are the advantages of molecular sieves in industrial gas drying?
In industrial gas drying, molecular sieves effectively remove water vapor, preventing moisture-related issues like corrosion, ice formation, and reduced equipment lifespan.
Are molecular sieves environmentally friendly?
Yes, molecular sieves contribute to environmental protection by reducing emissions, adsorbing VOCs and pollutants, and being reusable through regeneration processes.
What molecular sieve types are used for specific applications?
Types like 3A, 4A, 5A, and 13X are commonly used; for example, 3A is ideal for drying, 5A for nitrogen separation, and 13X for VOC adsorption in emissions control.
How are molecular sieves used in gas purification?
Molecular sieves remove contaminants, such as CO₂, H₂S, and other impurities, from gas streams, improving gas purity and protecting downstream equipment.
Why is hydrocarbon separation important in fuel refining?
Separating normal paraffins from isoparaffins using molecular sieves enhances fuel quality and efficiency, ensuring that refined products meet stringent standards.
What are the maintenance requirements for molecular sieves?
Regular monitoring and periodic regeneration are essential for maintaining molecular sieves’ effectiveness, especially in continuous industrial processes.
What factors should be considered when selecting a molecular sieve?
Considerations include pore size, adsorption capacity, compatibility with target molecules, regeneration method, and specific application requirements.
Where can I find detailed resources on molecular sieve applications?
For more insights on molecular sieve processes and applications, visit our Comprehensive Guide to Molecular Sieves.
“Molecular sieves drive purity and precision, ensuring quality, safety, and efficiency across diverse global applications.”
Conclusion
From gas separation to product preservation, molecular sieve processes perform essential functions across various industries. Their versatility makes them invaluable in enhancing gas purity, extending product life, and ensuring efficient, environmentally responsible operations. With their adaptability and durability, molecular sieves are
poised to meet the evolving demands of modern industry.
If you’re looking for specific molecular sieve products for these applications, browse our Molecular Sieves Product List. Whether for catalysis, adsorption, or PSA oxygen generation, we offer solutions tailored to your industry’s needs. For more foundational information on molecular sieves and their applications, refer to our cornerstone article A Comprehensive Guide to Molecular Sieve.
For more scientific resources, see Molecular Sieve on ScienceDirect.