Your Comprehensive Guide to Molecular Sieves 2024
Key Points | Description |
---|---|
Introduction | Molecular sieves are versatile materials used in various industries for their ability to separate and adsorb molecules. |
Types and Applications | Molecular sieves come in various types, including 3A, 4A, 5A, and 13X, each suited for different applications across various industries. |
How They Work | Molecular sieves function at the molecular level, with unique structures and adsorption properties. |
Industry Applications | Molecular sieves are used in the petrochemical, pharmaceutical, and food and beverage industries for various processes, including refining, purification, solvent drying, gas purification, and chromatography. |
Regeneration and Reuse | Molecular sieves can be regenerated and reused by heating them to remove the adsorbed molecules. |
Environmental Impact | Understanding the environmental impact of molecular sieves is crucial, and there are sustainable practices and alternatives available. |
Molecular Sieves vs. Silica Gel | Molecular sieves and silica gel are different types of desiccants, each with their own properties and performance characteristics. |
Advances in Technology and Research | There are ongoing advancements in molecular sieve technology and research, including new materials, manufacturing techniques, and applications. |
Troubleshooting | Common issues with molecular sieves, such as adsorption capacity loss, dust formation, and regeneration problems, can be addressed with proper troubleshooting. |
Product Range | SSE offers a wide range of high-quality molecular sieves in various types, sizes, and formats. |
Table of Contents
“Molecular sieves are like custom-fit filters—they only allow molecules of the perfect size to pass through.”
Introduction
Molecular sieves are an essential material for a wide range of industrial processes. They are microporous, synthetic materials made from zeolite, designed to adsorb gases or liquids based on their molecular size. This guide will help you understand what molecular sieves are, the different types available, and how to choose the best one for your needs.
Whether you’re in gas production, chemical processing, or another industry requiring precise moisture and impurity control, this guide will provide you with the knowledge to make an informed decision.
What Are Molecular Sieves?
Molecular sieves are adsorbents that contain tiny, uniform pores of fixed sizes. These pores allow the sieves to selectively adsorb gases or liquids based on their molecular diameter. The primary materials used in molecular sieves include zeolite or aluminosilicate, which have unique properties that make them effective for applications like gas separation and drying.
Key Features of Molecular Sieves
- High Adsorption Capacity: Molecular sieves have a high capacity for adsorbing moisture and other small molecules.
- Selective Molecule Separation: They selectively adsorb molecules based on their size.
- Available in Multiple Pore Sizes: Different pore sizes make them suitable for various industrial applications.
- Reusable After Regeneration: Molecular sieves can be regenerated and reused, making them cost-effective.
- Environmentally Friendly Material: Non-toxic and reusable, suitable for various industries.
Types of Molecular Sieves and Their Applications
For a detailed overview of the different types of molecular sieves and their specific applications, visit Molecular Sieves Types and Applications.
Molecular sieves come in various types, each with specific applications. Below is an overview of some of the most common types:
Molecular Sieve 3A
See Molecular Sieves 3A for more information
- Composition and Physical Properties: Made from potassium aluminosilicate, appearing as beige spherical beads in sizes 1.6-2.5 mm and 3.0-5.0 mm.
- Applications:
- Removing moisture from gases and liquids where minimal residual moisture is required.
- Gas drying, especially in the removal of moisture from hydrocarbons.
Molecular Sieve 4A
See Molecular Sieves 4A for more information
- Composition and Physical Properties: Contains sodium aluminosilicate, with a pore size of approximately 4 angstroms. Available in spherical beads of 1.6-2.5 mm or 3.0-5.0 mm.
- Applications:
- Suitable for separating CO2 and H2O impurities in gas mixtures.
- Commonly used for drying air, hydrocarbons, and solvents.
Molecular Sieve 5A
For more about how Molecular Sieves 5A are used in the petrochemical industry, visit Molecular Sieves in the Petrochemical Industry.
- Composition and Physical Properties: Sodium aluminosilicate-based, with a pore size of 5 angstroms.
- Applications:
- Used in PSA systems to separate normal and iso-paraffins.
- Effective in gas drying and deep solvent drying.
Molecular Sieve 13X
Learn more about the applications of molecular sieves in the pharmaceutical industry by visiting Molecular Sieves in the Pharmaceutical Industry.
For a look at the versatility of 13X molecular sieves, visit The Versatility of 13X Molecular Sieves.
- Composition and Physical Properties: Zeolite material with a pore size of approximately 9 angstroms. Typically used in spherical beads of size 1.6-2.5 mm.
- Applications:
- Separating gas components like nitrogen and oxygen in PSA systems.
- Deep drying of solvents, hydrocarbons, and petrochemicals.
Molecular Sieve MSOX-500 and MSOX-501
Molecular sieves also have unique uses in the food and beverage industry, particularly for maintaining product freshness and extending shelf life. Find out more at Molecular Sieves in the Food and Beverage Industry.
Discover the benefits of MSOX series molecular sieves for industrial applications by visiting The Power of MSOX Molecular Sieves.
- Composition and Physical Properties: Available in different sizes and designed for high-purity oxygen production. These sieves have a faster adsorption rate and longer service life.
- Applications:
- MSOX-500 is used in industrial and medical oxygen generators.
- MSOX-501 is intended for portable oxygen generators.
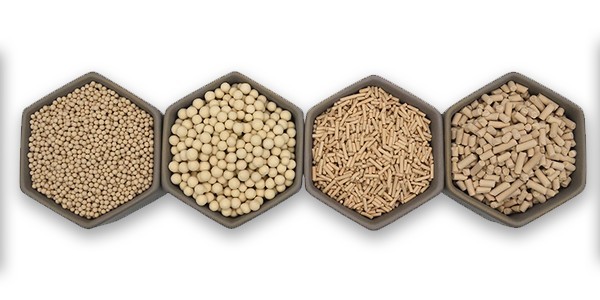
Types of Molecular Sieves
Type | Pore Size | Common Applications |
---|---|---|
3A | 3 Å | Dehydration of polar gases |
4A | 4 Å | Refrigerant drying |
5A | 5 Å | Natural gas purification |
13X | 10 Å | Air and gas separation |
How Molecular Sieves Work
Molecular sieves operate by trapping molecules within their structured framework. Due to their uniform pore size and high internal surface area, they are highly effective at adsorbing water and other impurities. The process involves exposing the sieve to gases or liquids, allowing only smaller molecules to enter the pores while excluding larger ones. This makes molecular sieves indispensable for drying, purification, and separation processes.
Molecular sieves function through the principle of selective adsorption, a process that enables them to trap specific molecules while allowing others to pass based on size and polarity. This unique mechanism is what makes molecular sieves so effective in industries like water treatment, petrochemical refining, and gas purification. Their precise pore structures allow them to isolate contaminants at the molecular level, achieving high levels of purity across applications. To gain a deeper understanding of the science and mechanics behind how these sieves operate, explore our detailed overview on How Molecular Sieves Work.
Key Molecular Sieve Processes
Exploring Key Molecular Sieve Processes
Molecular sieves play a fundamental role in many industrial processes, contributing to efficiency, product quality, and sustainability. Key molecular sieve processes include gas separation, adsorption, gas drying, catalytic support, and more. Each process utilizes the unique properties of molecular sieves to achieve high-purity outputs, prevent moisture damage, and support complex chemical reactions.
For a detailed look into how these processes are applied across various industries, check out our in-depth guide on Key Molecular Sieve Processes. This resource covers the science behind each process, real-world applications, and the advantages molecular sieves bring to critical industrial operations.
Molecular Sieves for Air Drying and Purification: Enhancing Air Quality and Equipment Longevity Across Industries
Molecular Sieves for Air Drying utilize advanced adsorption techniques to capture moisture and impurities efficiently. Their selective adsorption mechanism—choosing only specific molecules to bind—makes them a preferred choice in applications requiring precise moisture control. Industries that rely on compressed air, such as food processing and pharmaceutical production, benefit significantly from this technology, as molecular sieves ensure consistent, clean air output.
As industries evolve, the demand for high-purity air and moisture control grows, pushing molecular sieve technology toward greater innovation. The future of molecular sieves in air drying and purification lies in enhanced adsorption capacity, improved energy efficiency, and sustainable practices that support the increasing emphasis on clean, eco-friendly industrial solutions. For a closer look, explore the complete Molecular Sieves for Air Drying and Purification post.
Air Drying in Sulfonation: Ensuring Optimal Moisture Control
In sulfonation processes, precise moisture control is crucial to achieving high-quality outcomes. The presence of even minimal moisture can interfere with sulfonation reactions, leading to unwanted by-products and reduced efficiency. Air drying plays a vital role in this process by using desiccants to create the ideal low-humidity environment necessary for optimal reaction conditions.
While molecular sieves are a popular choice for moisture control due to their high adsorption capacity, other desiccants, like Activated Alumina, also serve effectively in certain applications. Each offers unique benefits depending on the specific requirements of the air drying system.
To dive deeper into the importance of air drying for sulfonation and explore best practices for maintaining low humidity, read our dedicated article: Achieving the Perfect Dry: Air Drying in Sulfonation.
Gas Separation with Molecular Sieves
Gas separation is a fundamental application of molecular sieves, particularly in processes requiring high-purity gases. Through selective adsorption, molecular sieves like 5A and MSOX can effectively separate gases such as nitrogen and oxygen by capturing one type of molecule while allowing the other to pass through. This process is widely used in industries that require specific gas streams, such as medical oxygen production and industrial nitrogen generation.
To explore the science behind gas separation and see specific industry applications in more detail, check out our in-depth article on Gas Separation with Molecular Sieve.
Hydrogen Purification and Clean Energy Applications
Hydrogen purification has become increasingly critical as industries shift toward clean energy sources. Molecular sieves play an essential role in achieving high-purity hydrogen, especially in applications where impurities like CO and CO₂ must be carefully removed to support fuel cell efficiency and sustainability initiatives. For a deeper look at how molecular sieves enable efficient hydrogen purification and enhance green energy efforts, visit our page on Molecular Sieves for Hydrogen Purification.
Pressure Swing Adsorption (PSA) for Oxygen Concentration
Pressure Swing Adsorption (PSA) is a critical process in separating and purifying gases, particularly for producing concentrated oxygen for medical and industrial applications. Using molecular sieves like 5A and specialized MSOX types, the PSA process enables efficient oxygen-nitrogen separation by adsorbing nitrogen under high pressure and releasing it under lower pressure, leaving behind high-purity oxygen.
This process is essential in healthcare for oxygen concentrators and is also widely used in industries requiring oxygen-rich environments. For a closer look at the science behind PSA and the role of molecular sieves in oxygen concentration, explore our detailed article on The Science of PSA Oxygen Concentration.
Adsorption Solutions with Molecular Sieves: Targeting VOCs, Ammonia, and Sulfur Compounds
In industries where purity and safety are essential, molecular sieves are powerful tools for selective adsorption of specific compounds, such as volatile organic compounds (VOCs), ammonia, and sulfur-based gases. Each of these compounds poses unique challenges, from controlling emissions to maintaining equipment integrity.
To learn more about targeted adsorption solutions with molecular sieves, which help capture VOCs, ammonia, and sulfur compounds efficiently, visit our detailed guide on Adsorption Solutions with Molecular Sieves.
Molecular Sieves and Their Role in Carbon Capture
Molecular sieves are vital in carbon capture and environmental sustainability, offering industries a powerful solution to reduce CO₂ emissions and control pollutants through selective adsorption. With uniform pore structures, sieves like 13X excel in CO₂ capture, especially within pressure swing adsorption (PSA) systems, where high-capacity CO₂ removal is essential. Additionally, 5A molecular sieves target both moisture and CO₂, enhancing hydrogen purification and biogas upgrading processes. By enabling eco-friendly filtration across automotive, energy, and petrochemical sectors, molecular sieves help produce cleaner fuels, control emissions, and improve operational efficiency. To learn more about these specific applications, explore our resource on Molecular Sieves for Carbon Capture.
Optimizing Gas Purity with Molecular Sieves
Achieving high gas purity is essential across various industries—from healthcare to petrochemical processing—where contaminants can impact both product quality and operational safety. Molecular sieves play a crucial role in this by selectively adsorbing specific molecules, ensuring gases like oxygen, nitrogen, and natural gas reach the required purity levels. Through processes like gas separation, gas drying, and gas purification, molecular sieves provide versatile solutions that meet industry standards.
For a comprehensive look at how molecular sieves are used to optimize gas purity and enhance efficiency, explore our in-depth guide on Optimizing Gas Purity.
Karl Fischer Titration
Karl Fischer Titration is a widely recognized analytical technique used to measure water content in various materials with exceptional accuracy. The method involves a chemical reaction between water and Karl Fischer reagent, producing a measurable electrical endpoint that determines the exact moisture level. This technique is essential in industries such as pharmaceuticals, petrochemicals, and food processing, where precise moisture analysis ensures product quality and compliance with regulatory standards. By maintaining moisture-free conditions with molecular sieves, Karl Fischer Titration achieves unparalleled accuracy in detecting even trace amounts of water.
Molecular Sieves for Karl Fischer Titration ensure precise moisture analysis by stabilizing reagents and enhancing accuracy. Discover how their advanced adsorption properties optimize titration processes, improve reagent longevity, and support critical applications in diverse industries.
Read more here: Molecular Sieves for Karl Fischer Titration: Enhancing Accuracy in Moisture Analysis
Applications in Specific Industries
Petrochemical and Refining
Molecular sieves are indispensable in the petrochemical and refining industries, especially for hydrocarbon separation. They improve fuel quality by selectively adsorbing specific molecules such as sulfur compounds, VOCs, and aromatics. This selective adsorption leads to cleaner-burning, high-efficiency fuels essential for meeting environmental standards and performance goals. Molecular sieves like 3A and 5A are particularly effective in enhancing fuel purity by precisely targeting and removing unwanted compounds.
For a detailed exploration of how molecular sieves enhance fuel quality in refining, visit our guide on Hydrocarbon Separation and Refining: How Molecular Sieves Enhance Fuel Quality.
Biofuels and Renewable Energy
In the renewable energy sector, particularly in biofuel production, molecular sieves are critical for achieving the high-purity ethanol needed for fuel-grade applications. The ethanol dehydration process relies on molecular sieves to remove water from ethanol, yielding a cleaner-burning fuel compatible with strict environmental standards. Ethanol dehydration with molecular sieves not only enhances fuel quality but also supports biofuel producers in meeting sustainability targets.
For a closer look at how molecular sieves are transforming ethanol production, visit Molecular Sieves for Ethanol Dehydration: Ensuring Purity and Efficiency.
Pharmaceutical Industry
Molecular sieves play a vital role in the pharmaceutical industry, where high purity and moisture control are essential. Their selective adsorption capabilities ensure the removal of impurities and the preservation of product stability, which is critical in pharmaceutical production. The 13X molecular sieve, with its high adsorption capacity, is widely utilized here, particularly for stabilizing catalysts in reaction processes and producing cleaner, high-purity products. Explore more applications in our post on Molecular Sieves in the Pharmaceutical Industry.
Food and Beverage Industry
In the food and beverage industry, molecular sieves contribute significantly to moisture control and freshness preservation. By effectively adsorbing moisture and certain impurities, molecular sieves extend product shelf life and help maintain quality standards, making them essential for food storage and processing. Discover how molecular sieves support the food and beverage sector in Molecular Sieves in the Food and Beverage Industry.
Water Treatment
Water treatment is another critical area where molecular sieves have proven to be invaluable. With their unique selective adsorption capabilities, molecular sieves can effectively capture and remove contaminants such as heavy metals, VOCs, and dissolved gases from water. This makes them a preferred choice in municipal water treatment facilities, industrial wastewater purification, and agricultural runoff management. For an in-depth look at how molecular sieves ensure water quality and regulatory compliance, visit our guide on Molecular Sieves in Water Treatment: Ensuring Safe, Clean Water.
Catalyst Support in Petrochemical Applications
Molecular sieves, particularly the 13X variety, are widely used as catalyst supports due to their large pore size and high adsorption capacity. They stabilize catalysts and enhance reaction efficiencies, especially in the production of cleaner fuels and high-purity chemicals. This capability is vital for processes requiring precise reaction conditions. To learn more about the benefits of 13X molecular sieves as catalyst supports, visit Molecular Sieve 13X Catalyst Support.
Gas Separation and PSA Systems
Molecular sieves are critical in gas separation processes, especially in Pressure Swing Adsorption (PSA) systems used to produce high-purity gases such as oxygen and nitrogen. PSA relies on the selective adsorption properties of molecular sieves to capture specific gases under varying pressure conditions. Molecular sieve types like 5A and 13X are integral to PSA processes, ensuring optimal gas purity and efficiency. Explore our guide on Pressure Swing Adsorption for a deeper dive into this application.
Industrial Gas Purification
The selective adsorption capabilities of molecular sieves are essential in industrial gas purification, where they capture gases such as carbon dioxide (CO₂) and nitrogen (N₂). By targeting these compounds, molecular sieves help reduce greenhouse gas emissions and achieve high-purity gas streams for specialized applications. Molecular sieves like 13X excel in CO₂ and N₂ adsorption, making them suitable for chemical processing, medical applications, and environmental management. Learn more in our guide on CO₂ Adsorption and N₂ Adsorption.
Molecular Sieves in Refrigeration: Enhancing Efficiency and Longevity
In refrigerant systems, effective moisture control is critical for maintaining optimal performance, preventing ice formation, and extending equipment lifespan. Molecular Sieves for Refrigerants play a key role in achieving these goals by acting as highly efficient desiccants designed specifically for HVAC and cooling systems. With specialized molecular sieves, refrigerant systems experience reduced risk of ice blockage, minimized corrosion, and better refrigerant drying efficiency, ultimately leading to more reliable and sustainable operations. Discover the detailed benefits and applications of molecular sieves in refrigerant systems in our dedicated post.
Molecular Sieves for Truck Air Brakes
An important niche within molecular sieve applications, Molecular Sieves for Truck Air Brakes provide an essential solution for moisture management in the compressed air systems used in heavy vehicles. These sieves work by adsorbing excess moisture, preventing ice formation and corrosion that can compromise brake reliability and safety. For trucks and heavy-duty vehicles that rely on air brakes, using molecular sieves extends brake lifespan and boosts operational safety, particularly in extreme weather conditions.
Explore our in-depth post on Molecular Sieves for Truck Air Brakes to learn how this technology is transforming brake maintenance and enhancing transportation safety.
Molecular Sieves in Healthcare: Medical-Grade Oxygen Production
In medical applications, molecular sieves play a critical role in ensuring oxygen purity and reliability, especially within PSA oxygen concentrators. By effectively separating nitrogen, these sieves produce the high-quality, medical-grade oxygen that healthcare facilities rely on daily. For an in-depth look into the importance and technical specifics of molecular sieves in this field, explore our guide on Molecular Sieves for Medical Oxygen Production.
Adsorption Properties of Molecular Sieves
Property | Impact |
---|---|
Selectivity | Adsorbs molecules selectively |
Adsorption Rate | Depends on pore size and pressure |
Temperature Tolerance | Can withstand high temperatures |
Advantages of Molecular-Level Adsorption
- Removes even trace moisture.
- Highly specific to molecule size.
- Effective in both gas and liquid phases.
Choosing the Right Molecular Sieve for Your Application
Selecting the appropriate molecular sieve is critical to achieving optimal performance in industrial applications. Whether you’re focused on gas drying, gas separation, or maintaining high purity levels, choosing the right molecular sieve will ensure efficiency and cost-effectiveness. Here’s a comprehensive guide to help you select the right type, along with additional resources for deeper insights.
1. Gas Drying: Achieving Optimal Moisture Control
For applications involving gas drying—particularly in hydrocarbon streams—Molecular Sieve 3A is a preferred option. This sieve type is excellent for minimizing residual moisture, thanks to its selective adsorption of small molecules. For industries looking to compare various desiccant options, including activated alumina and silica gel, our guide on Choosing the Right Desiccant for Compressed Air Systems offers valuable insights into which materials best fit different drying applications.
2. PSA Applications: High-Efficiency Gas Separation
If you require gas separation within Pressure Swing Adsorption (PSA) units, Molecular Sieve 5A or 13X are recommended choices. These types are specifically engineered for separating gases based on molecular size and affinity. Molecular Sieve 5A is widely used for separating nitrogen from oxygen, while 13X excels in capturing larger molecules, such as CO₂, making it highly effective in air separation and oxygen concentrators. For applications that demand high-purity gas production, choosing the correct sieve for PSA can lead to superior performance and purity.
3. High-Purity Oxygen Production
For oxygen generation, especially in medical or high-purity industrial applications, MSOX-500 and MSOX-501 molecular sieves are the top options. These molecular sieves are optimized for oxygen concentrators and generators, providing high efficiency, long lifespan, and excellent regeneration capabilities. Their design enables a faster adsorption rate, making them well-suited for systems where consistent oxygen purity is essential.
4. Molecular Sieves vs. Silica Gel: Understanding the Differences
For users deciding between molecular sieves and silica gel, it’s essential to recognize the unique properties and strengths of each. Molecular sieves offer superior selectivity and can achieve lower dew points than silica gel, making them more effective in applications where precise moisture control is required. Silica gel, on the other hand, is a versatile desiccant ideal for less critical moisture control applications. Visit our Molecular Sieves vs. Silica Gel page for a detailed comparison to help you make an informed choice.
5. Troubleshooting and Maintenance: Ensuring Longevity and Performance
Even with the right choice of molecular sieve, operational challenges can arise, impacting the efficiency of your system. Common issues include adsorption capacity loss, dust formation, and regeneration problems. Our guide on Troubleshooting Common Issues with Molecular Sieves provides practical solutions to address these challenges, ensuring that your molecular sieve performs optimally throughout its lifecycle.
By carefully selecting the right molecular sieve and using available troubleshooting and comparison resources, industries can achieve targeted results, from gas drying to advanced PSA applications. This strategic approach ensures that each molecular sieve type is used where it performs best, leading to greater efficiency, longevity, and purity across applications.
Regeneration and Reuse of Molecular Sieves
Molecular sieves are known for their reusability, and proper regeneration methods ensure their efficiency and longevity. By understanding and applying the right regeneration techniques, industries can significantly enhance the lifespan of their molecular sieves, making them a cost-effective and sustainable choice in various applications. Below are key methods and benefits associated with molecular sieve regeneration.
Regeneration Methods
- Heat Treatment: Heat treatment is one of the most commonly used regeneration methods, where molecular sieves are heated to a specific temperature to release adsorbed contaminants. This process restores the sieves to their original adsorption capacity, making them ready for reuse. For example, heating molecular sieves to around 200-300°C can effectively remove moisture, hydrocarbons, and other volatile compounds.
- Vacuum Desorption: In vacuum desorption, a vacuum is applied to the molecular sieve to reduce the pressure and release adsorbed molecules. This method is particularly effective for removing gases and can be combined with heat to improve regeneration efficiency.
- Steam Reuse: In some cases, steam is applied to molecular sieves to remove specific contaminants, especially in applications involving the removal of organic compounds. This method is advantageous for sieves that require gentle, low-temperature regeneration.
For a deeper understanding of these processes, our guide on Regeneration and Reuse of Molecular Sieves provides detailed insights into the methods and best practices to ensure optimal performance and longevity.
Benefits of Regeneration
- Extended Lifespan: Regular regeneration greatly extends the lifespan of molecular sieves, making them a reliable long-term investment.
- Cost Efficiency: By regenerating and reusing molecular sieves, industries reduce the need for frequent replacements, resulting in substantial cost savings.
- Improved Performance: Regenerated sieves maintain their adsorption capacity, ensuring high efficiency in applications where consistent quality is crucial.
- Reduced Environmental Impact: Reusing molecular sieves reduces waste and minimizes environmental impact, supporting sustainable practices across industries.
Regular regeneration not only maintains adsorption efficiency but also contributes to a greener, more economical operation. For more details on regeneration techniques and their benefits, visit Regeneration and Reuse of Molecular Sieves.
Environmental Impact of Molecular Sieves
The environmental impact of molecular sieves is an important consideration for industries committed to sustainable practices. Molecular sieves, by nature, are designed for repeated use and can contribute positively to reducing waste in industrial applications. However, maximizing their eco-friendly potential involves adopting best practices and exploring new advancements in the field.
Sustainable Practices and Alternatives
- Eco-Friendly Regeneration: Regenerating molecular sieves through low-energy methods, such as vacuum desorption or controlled heat treatment, reduces energy consumption and carbon emissions. Using eco-friendly regeneration methods can make molecular sieves a more sustainable choice for industries seeking to lower their environmental footprint.
- Reduced Chemical Use: Unlike some chemical treatment methods, molecular sieves work through physical adsorption, minimizing the need for chemical additives and reducing the risk of chemical discharge into the environment. This clean approach makes molecular sieves safer for use in environmentally sensitive applications like water treatment.
- Advances in Molecular Sieve Technology: Emerging innovations are focusing on developing molecular sieves with higher adsorption efficiency and better selectivity, which can further reduce environmental impact by optimizing performance and requiring less frequent regeneration. For instance, advancements in pore structure design and material composition allow for more targeted adsorption, reducing waste and enhancing sustainability. To explore ongoing innovations, see our article on Advances in Molecular Sieve Technology and Research.
Further Reading: Environmental Insights
To understand the full scope of molecular sieves’ environmental impact, including their advantages in sustainable industrial practices, see our guide on The Environmental Impact of Molecular Sieves. This resource covers how molecular sieves compare to other desiccants, their role in reducing emissions, and the potential for eco-friendly applications in various sectors.
By combining sustainable practices and adopting the latest advancements in molecular sieve technology, industries can continue to benefit from high-performance adsorption while supporting eco-friendly initiatives.
Environmental Benefits of Molecular Sieves
Benefit | Description |
---|---|
Reduced Emissions | Adsorbs harmful gases in industries |
Non-toxic | Safe for use in food and beverage |
Reusability | Reduces overall environmental footprint |
Packaging and Storage of Molecular Sieves
Proper packaging and storage of molecular sieves are essential to preserving their effectiveness and ensuring that they are ready for use in various applications. When stored correctly, molecular sieves can maintain their adsorption capacity for extended periods, allowing industries to rely on their performance without degradation. Here, we outline essential storage tips, options, and best practices.
Storage Tips and Options
- Airtight Packaging: Molecular sieves are highly hygroscopic, meaning they readily adsorb moisture from the surrounding environment. To prevent premature saturation, it is crucial to store them in airtight containers or sealed packaging. Options like moisture-proof bags, sealed plastic drums, or vacuum-sealed pouches are effective in maintaining the sieves’ dryness.
- Controlled Environment: Ideally, molecular sieves should be stored in a cool, dry area with minimal humidity. High humidity levels can cause the sieves to adsorb moisture from the air, which could reduce their efficiency when needed for actual applications. For this reason, storing molecular sieves in a climate-controlled environment, away from direct sunlight and heat sources, is recommended.
- Bulk Storage Solutions: For industrial settings that require large quantities of molecular sieves, bulk storage options such as sealed steel drums or plastic-lined fiber drums are practical solutions. These containers prevent moisture ingress and allow easy access for refilling or replacing sieves in process units.
- Use of Desiccant Packs: For smaller quantities or storage over an extended period, desiccant packs can be added to storage containers to absorb any residual moisture. This adds an extra layer of protection to ensure that the molecular sieves remain in optimal condition.
- Avoid Frequent Exposure: Every time molecular sieves are exposed to open air, they begin adsorbing moisture, which can quickly reduce their capacity. For operations where sieves are frequently accessed, consider only opening the storage container when necessary and sealing it immediately after to limit moisture exposure.
For an in-depth look at best practices in handling, packaging, and storage, refer to our dedicated article on Packaging and Storage of Molecular Sieves. This guide provides detailed insights into packaging options and methods to ensure your molecular sieves are always ready for high-performance adsorption.
Benefits of Proper Packaging and Storage
- Extended Shelf Life: Correct packaging extends the functional life of molecular sieves, making them ready to use when required and reducing wastage.
- Cost Efficiency: By minimizing premature adsorption and maintaining their quality, you reduce the need for frequent replacements, optimizing the overall cost of ownership.
- Enhanced Performance: Properly stored molecular sieves perform more reliably, providing consistent adsorption capacity in critical applications.
By implementing these packaging and storage techniques, industries can maximize the effectiveness and longevity of their molecular sieves, ensuring dependable results across various applications. For more details, please visit Packaging and Storage of Molecular Sieves.
Molecular Sieve
Property | Description |
---|---|
Type | Zeolite 3A, 4A, 5A, 13X |
Application Areas | Petrochemicals, Pharmaceuticals |
Adsorption Type | Molecular level separation |
Regeneration | Heat-based recovery process |
Environmental Role | Adsorb contaminants, eco-friendly |
Our Product Range
At SSE, we understand the importance of finding the right molecular sieve product for your specific needs. That’s why we offer a wide range of high-quality molecular sieves in various types, sizes, and formats, ensuring optimal performance and efficiency for your applications.
Our Molecular Sieve Products
We offer a wide range of Molecular Sieves designed for various industrial applications. Here is a list of our products along with a brief description of each:
- Molecular Sieve 3A (1.6-2.5 mm, 150 kg Drum): Ideal for moisture removal in gas streams, preventing contamination by adsorbing molecules with effective diameters smaller than 3 angstroms.
- Molecular Sieve 3A (1.6-2.5 mm, 30 kg Drum): A versatile desiccant suitable for drying unsaturated hydrocarbons like ethylene and propylene.
- Molecular Sieve 3A (3-5 mm, 150 kg Drum): Perfect for dehydration processes in insulating glass units and other polar compounds.
- Molecular Sieve 3A (3-5 mm, 30 kg Drum): Specialized for static dehydration, particularly in air- or gas-filled insulating glass units.
- Molecular Sieve 4A (1.6-2.5 mm, 150 kg Drum): Efficient for removing CO2, ammonia, and hydrocarbons from natural gas and other gas streams.
- Molecular Sieve 4A (1.6-2.5 mm, 30 kg Drum): Suitable for use in refrigeration dehydration and air brakes for transport vehicles.
- Molecular Sieve 4A (3-5 mm, 150 kg Drum): Commonly used for gas purification, removing contaminants from LPG, air, and other gases.
- Molecular Sieve 4A (3-5 mm, 30 kg Drum): Packaged for convenient use as a food-grade desiccant.
- Molecular Sieve 5A (1.6-2.5 mm, 150 kg Drum): Suitable for PSA applications, including hydrogen and oxygen purification.
- Molecular Sieve 5A (1.6-2.5 mm, 30 kg Drum): Ideal for separating normal- and iso-paraffins and other mixed gas applications.
- Molecular Sieve 5A (3.0-5.0 mm, 150 kg Drum): Designed for gas drying and purification in various industrial processes.
- Molecular Sieve 5A (3.0-5.0 mm, 30 kg Drum): Effective for refining processes, including separation of paraffins.
- Molecular Sieve 13X (125 kg Drum): Used for CO2 and moisture removal from air and other gases, especially in air separation plants.
- Molecular Sieve 13X (1.6-2.5 mm, 125 kg Drum): Ideal for general dehydration and CO2 removal in gas streams.
- Oxygen Molecular Sieve MSOX500 PSA (125 kg Drum): Specialized for PSA oxygen generation, ensuring high purity oxygen production.
- Molecular Sieve MSOX-500 & MSOX-501: Advanced PSA technology for high-purity oxygen production, offering efficiency and reliability.
To explore our entire range of molecular sieves and find the perfect product for your needs, visit our molecular sieve product category. At SSE, we are committed to providing high-quality, reliable molecular sieves that deliver exceptional performance for all your applications.
Frequently Asked Questions
What are molecular sieves?
Molecular sieves are highly porous, crystalline aluminosilicate materials that are commonly used as adsorbents in various industrial processes. They can effectively separate molecules based on their size and shape, making them ideal for a wide range of applications, such as gas and liquid purification, dehydration, and separation.
What types of molecular sieves does SSE offer?
SSE offers a variety of molecular sieve types, including 3A, 4A, 5A, and 13X. We also provide specialty molecular sieves like MSOX-500 and MSOX-501 for specific applications in oxygen generation.
How do I choose the right molecular sieve for my application?
The choice of molecular sieve depends on your specific application requirements, such as the type of molecules you need to adsorb, the operating conditions, and the desired level of purification. Consult with a packaging expert or our team for guidance on selecting the appropriate molecular sieve for your needs.
Can molecular sieves be reused?
Yes, molecular sieves can often be regenerated and reused by heating them to remove the adsorbed molecules. However, the regeneration process may vary depending on the type of molecular sieve and the specific application. It is essential to follow the manufacturer’s guidelines for proper regeneration and reuse.
What is the difference between 3A, 4A, 5A, and 13X molecular sieves?
The primary difference between these molecular sieves is their pore size, which determines the types of molecules they can adsorb. 3A molecular sieves have a pore size of approximately 3 angstroms, 4A sieves have a 4-angstrom pore size, 5A sieves have a 5-angstrom pore size, and 13X sieves have a larger pore size of approximately 10 angstroms. Each type of molecular sieve is suited for different applications, depending on the size and shape of the molecules being separated.
What are MSOX-500 and MSOX-501 molecular sieves used for?
MSOX-500 and MSOX-501 are specialty molecular sieves designed specifically for oxygen generation in medical and industrial applications. They are highly effective in separating oxygen from air, resulting in high-purity oxygen suitable for various uses.
How do I store unused molecular sieves?
Unused molecular sieves should be stored in an airtight container to prevent exposure to moisture and air. This will help maintain their effectiveness and prolong their shelf life.
Can I use molecular sieves in combination with other purification methods?
Yes, molecular sieves can be used in conjunction with other purification methods, such as activated carbon, silica gel, or other adsorbents, to achieve the desired level of purification and separation in your specific application.
Conclusion: Exploring the World of Molecular Sieves
Molecular sieves are versatile and effective for various applications in gas separation, drying, and purification. By selecting the right type, you can ensure efficient processing tailored to your needs. If you have more questions or need further assistance, feel free to contact us. We’re here to help you make the right choice for your business.
External links
https://www.sciencedirect.com/topics/chemistry/molecular-sieve
https://www.sciencedirect.com/science/article/abs/pii/S092422442030488X